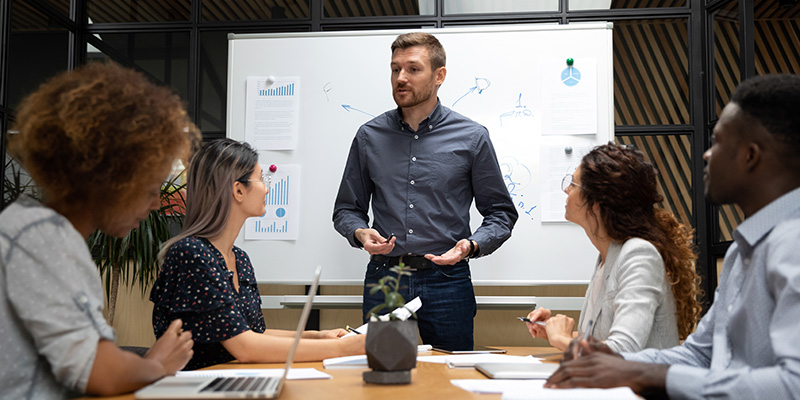
Consistency between contracts is crucial for construction projects involving multiple parties. Prime contracts often contain provisions that are passed on to subcontractors and other sub-subcontractors. To ensure that all agreements align, it is vital for parties involved in a project.
Order for a Job
Job order contractual (JOC) can be used to manage project costs and time. It is an efficient way to clear backlogs of deferred work and respond quickly to ongoing projects. JOC is flexible and more flexible than other contracting models.
The job order contracting system makes the project owner and contractor more transparent right from the start. They have a common understanding of each other's past and work history, which allows them to trust each other. This reduces the need for change orders. The owner and contractor will have a greater understanding of each others' work, which can help them to build a stronger partnership. This prevents miscommunications and errors from causing many changes.
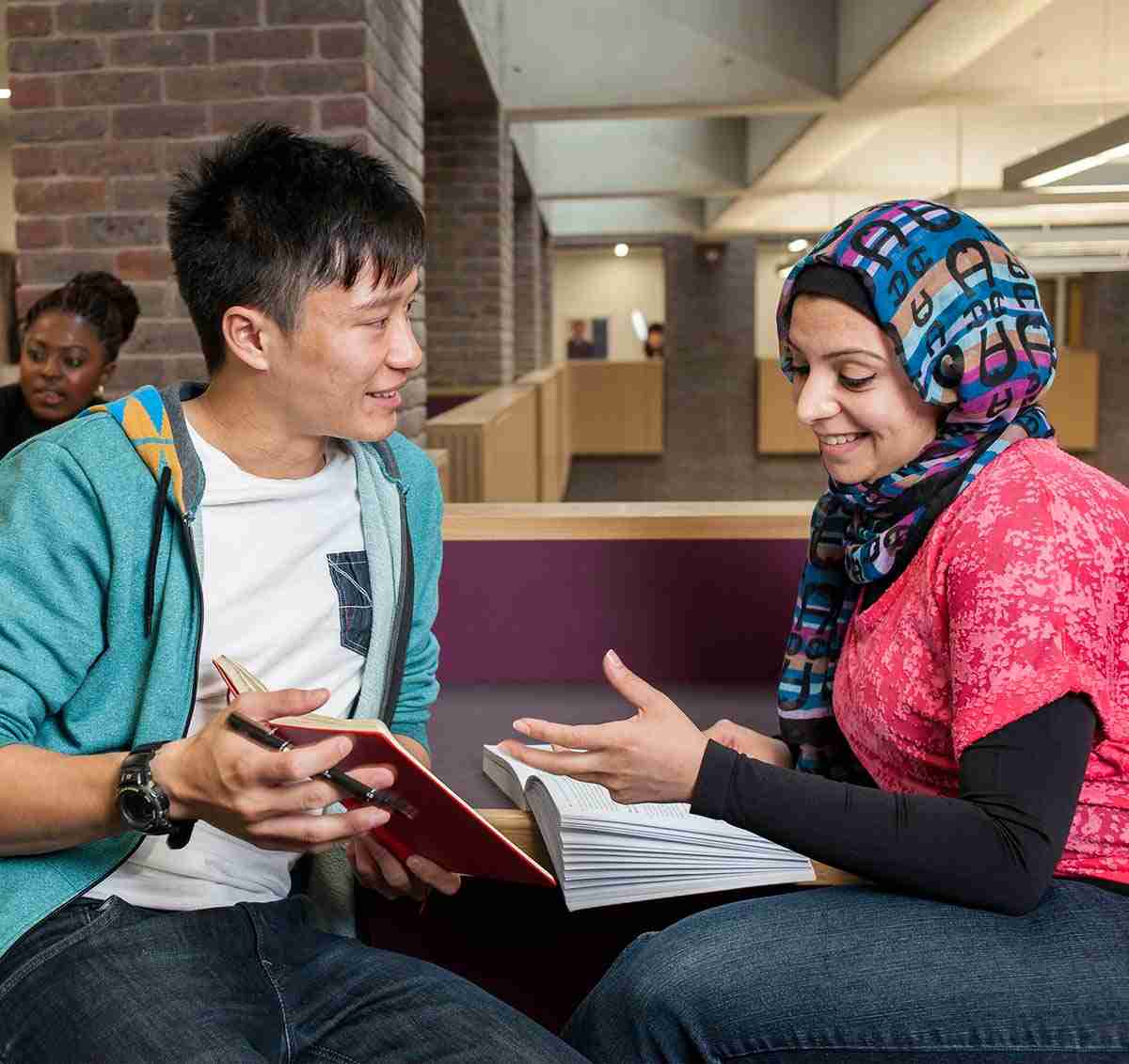
Incentive
Incentive contracting is a type of collaboration between a contractor and the client. The goal is to maximize the value of money. Two main components of an incentive contract are a target costs and a formula. The target cost is agreed upon through a competitive procedure, and should reflect the most accurate estimate of the project's outturn costs. The contractor gets paid a fee that covers their overheads. The share formula introduces an incentive to the contract and determines how much should be divided between the parties.
One major benefit of incentive contracts is that it creates an environment of accountability and transparency. Contractors are more likely be to give owners timely updates when they are fully aware of the work in process. These updates promote closer cooperation and encourage the assignment of skilled personnel.
Lump-sum
Lump-sum contracting for construction is a form of contracting that involves a fixed amount of money being agreed upon from the beginning. This type of contract involves a fixed target, inputs, and outputs. This type of contract is most effective when the project is clearly defined and has little variability. However, lump-sum contracts have some drawbacks.
A contractor may hide his profit margins by not being transparent. Contractors do not have to submit detailed estimates or bills of cost to the owner. One disadvantage to lump-sum contracts are that they can be subject to disputes or claims arising from poor contract terms. One example is when a contractor produces an unbalanced bid. In this case, unit prices may be increased for items that will be used later in a project. This can lead to disputes over payment rates.
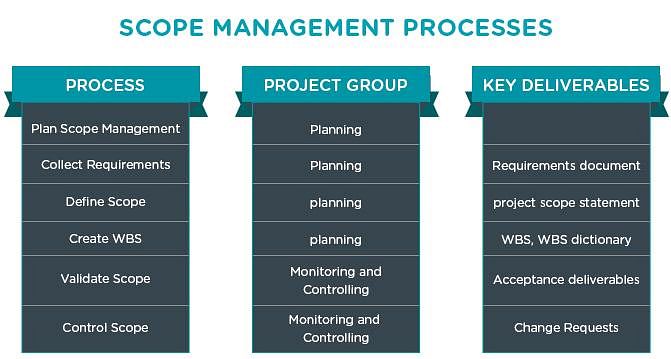
Delivery of integrated projects
Integrated Project Delivery (or IPD) is a new method of delivering construction projects. It removes the barriers that prevent project performance and brings together stakeholders to achieve a common goal. It improves the chances of projects succeeding. Implementing IPD involves a complete overhaul of existing project management processes and greater planning. Some of the major barriers to IPD include legal concerns, mistrust among key parties, and a lack of owner willingness. Many professionals and organizations working in the built environment are now aware of the benefits IPD has and are starting to implement the concept in smaller projects.
IPD offers the opportunity to reduce costs and speed up projects. It allows all stakeholders to be more focused on what they do best. This results in greater client satisfaction.
FAQ
Six Sigma is so popular.
Six Sigma can be implemented quickly and produce impressive results. Six Sigma also gives companies a framework for measuring improvement and helps them focus on what is most important.
What are the main styles of management?
There are three main management styles: participative, laissez-faire and authoritarian. Each style has strengths and flaws. Which style do YOU prefer? Why?
Autoritarian – The leader sets the direction for everyone and expects them to follow. This style is best when the organization has a large and stable workforce.
Laissez faire - Each individual can decide for himself/herself. This style is most effective when the organization's size and dynamics are small.
Participative – Leaders are open to suggestions and ideas from everyone. This approach works best in small organizations where everyone feels valued.
What is a fundamental management tool for decision-making?
The decision matrix is a powerful tool that managers can use to help them make decisions. It helps them to think strategically about all options.
A decision matrix represents alternatives in rows and columns. This makes it easy to see how each alternative affects other choices.
We have four options in this example. They are represented by the boxes to the left of the matrix. Each box represents an alternative. The top row depicts the current status quo, while the bottom row represents what would happen if no action was taken.
The effect of Option 1 can be seen in the middle column. In this example, it would lead to an increase in sales of between $2 million and $3 million.
The results of choosing Option 2 and 3 can be seen in the columns below. These are positive changes - they increase sales by $1 million and $500 thousand respectively. These positive changes have their downsides. Option 2, for example, increases the cost by $100 000 while Option 3 decreases profits by $200 000.
The final column shows the results for Option 4. This involves decreasing sales by $1 million.
The best thing about a decision matrix is the fact that you don't have to remember which numbers go with what. You can just glance at the cells and see immediately if one given choice is better.
This is because the matrix has already taken care of the hard work for you. It's as easy as comparing numbers in the appropriate cells.
Here is an example how you might use the decision matrix in your company.
You want to decide whether or not to invest more money into advertising. This will allow you to increase your revenue by $5000 per month. But, you will also incur additional expenses of $10 thousand per month.
You can calculate the net result of investing in advertising by looking at the cell directly below the one that says "Advertising." That number is $15 thousand. Advertising is a worthwhile investment because it has a higher return than the costs.
What are the steps involved in making a decision in management?
Managers face complex and multifaceted decision-making challenges. It involves many factors, including but not limited to analysis, strategy, planning, implementation, measurement, evaluation, feedback, etc.
Remember that people are humans just like you, and will make mistakes. This is the key to managing them. As such, there are always opportunities for improvement, especially when you put in the effort to improve yourself.
This video shows you how management makes decisions. We discuss the different types of decisions and why they are important, every manager should know how to navigate them. The following topics will be covered:
How does Six Sigma function?
Six Sigma employs statistical analysis to identify problems, measure them and analyze root causes. Six Sigma also uses experience to correct problems.
The first step is identifying the problem.
Next, data are collected and analyzed in order to identify patterns and trends.
Next, corrective steps are taken to fix the problem.
Final analysis of data is done to determine if the problem has been solved.
This continues until you solve the problem.
Statistics
- Your choice in Step 5 may very likely be the same or similar to the alternative you placed at the top of your list at the end of Step 4. (umassd.edu)
- UpCounsel accepts only the top 5 percent of lawyers on its site. (upcounsel.com)
- The average salary for financial advisors in 2021 is around $60,000 per year, with the top 10% of the profession making more than $111,000 per year. (wgu.edu)
- The profession is expected to grow 7% by 2028, a bit faster than the national average. (wgu.edu)
- Hire the top business lawyers and save up to 60% on legal fees (upcounsel.com)
External Links
How To
What is Lean Manufacturing?
Lean Manufacturing methods are used to reduce waste through structured processes. They were created by Toyota Motor Corporation in Japan in the 1980s. The aim was to produce better quality products at lower costs. Lean manufacturing seeks to eliminate unnecessary steps and activities in the production process. It is composed of five fundamental elements: continuous improvement; pull systems, continuous improvements, just-in–time, kaizen, continuous change, and 5S. Pull systems involve producing only what the customer wants without any extra work. Continuous improvement is the continuous improvement of existing processes. Just-in-time refers to when components and materials are delivered directly to the point where they are needed. Kaizen means continuous improvement. Kaizen involves making small changes and improving continuously. Last but not least, 5S is for sort. These five elements are used together to ensure the best possible results.
Lean Production System
The lean production system is based on six key concepts:
-
Flow is about moving material and information as near as customers can.
-
Value stream mapping - break down each stage of a process into discrete tasks and create a flowchart of the entire process;
-
Five S’s - Sorted, In Order. Shine. Standardize. And Sustain.
-
Kanban – visual signals like colored tape, stickers or other visual cues are used to keep track inventory.
-
Theory of Constraints - Identify bottlenecks in the process, and eliminate them using lean tools such kanban boards.
-
Just-in-time - deliver components and materials directly to the point of use;
-
Continuous improvement - Make incremental improvements rather than overhauling the entire process.