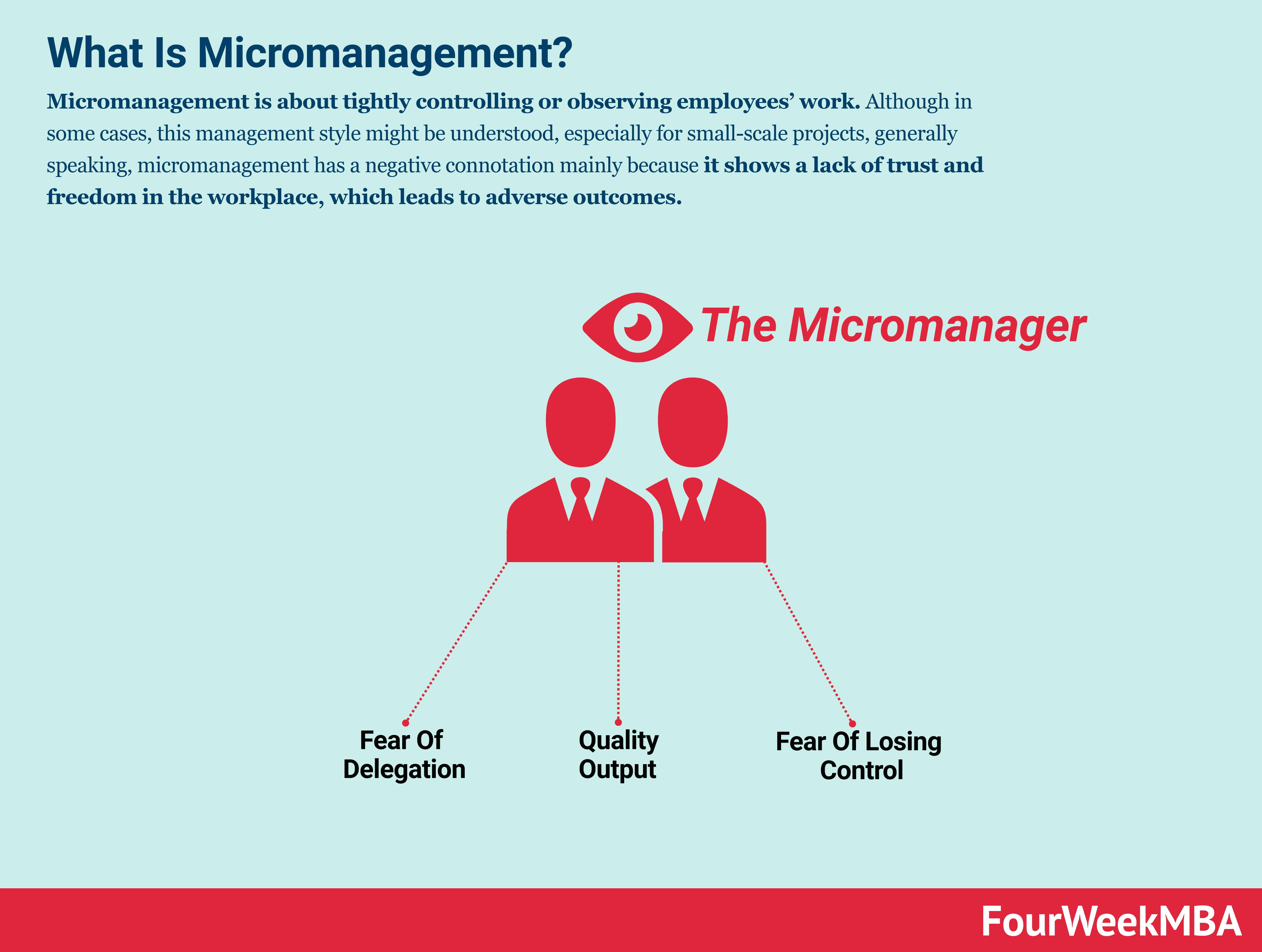
A team can find it difficult to follow a self-managed plan, but it can also make things easier. You will learn about the benefits and drawbacks of self-managed groups and how to implement them within your team. This article will help you make an informed decision about whether self managed teams are right for you. For a deeper discussion, continue reading.
Negatives of self managed teams
You have many advantages and disadvantages when you use self-managed team members in your business. Although the structure offers more flexibility, it can also lead to a vacuum of power in your team. Some people will assume the leadership role, while others will shirk their duties. Self-managed organizations are not held accountable for their performance. This makes it difficult to exert influence on the team by executives, which can lead to a lack in creativity and productivity.
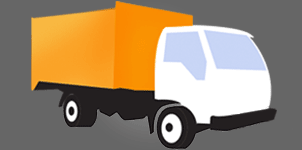
Self-managed team members can prove ineffective at enhancing organizational performance. This is one of the main disadvantages. Managers should clearly outline their responsibilities to their teams and delegate authority. This will make them more productive. Self-managed teams may not achieve the goals set by their managers. A manager should be a part of self-managed groups. He or she should hold the team responsible for their results and give feedback to members.
Challenges of self-managed teams
Self-managed teams have many advantages. These teams are typically more productive than traditional teams. They can share ideas quickly and move forward with their actions. These teams are more likely to be innovative as they assume responsibility for their own work. However, there are disadvantages. While self-managed teams may be a better option for some organizations, it is still essential to consider them before choosing them. We'll be looking at the challenges and benefits of self-managed team.
In addition to boosting team productivity, self-managed teams may also pose challenges to individual commitment. The problem with self-directed groups is that members may specialize in one area, which can limit collaboration and shared commitment. This problem can be alleviated by establishing a system in which team members can vote on a decision and agree on a course of action. Due to the lack cross-team communication, self-managed groups may not be as collaborative than traditional teams.
Here are some ways to make self-managed team members
One of the ways to implement self-managed teams is by creating a culture of accountability. Unlike traditional teams, where members take responsibility for individual decisions, self-managed teams are driven by commitments made by members. Because each member recognizes both his or her individual responsibilities, this makes it easier for the work to move forward. The team is encouraged to have a sense of accountability. This atmosphere of accountability fosters creativity.
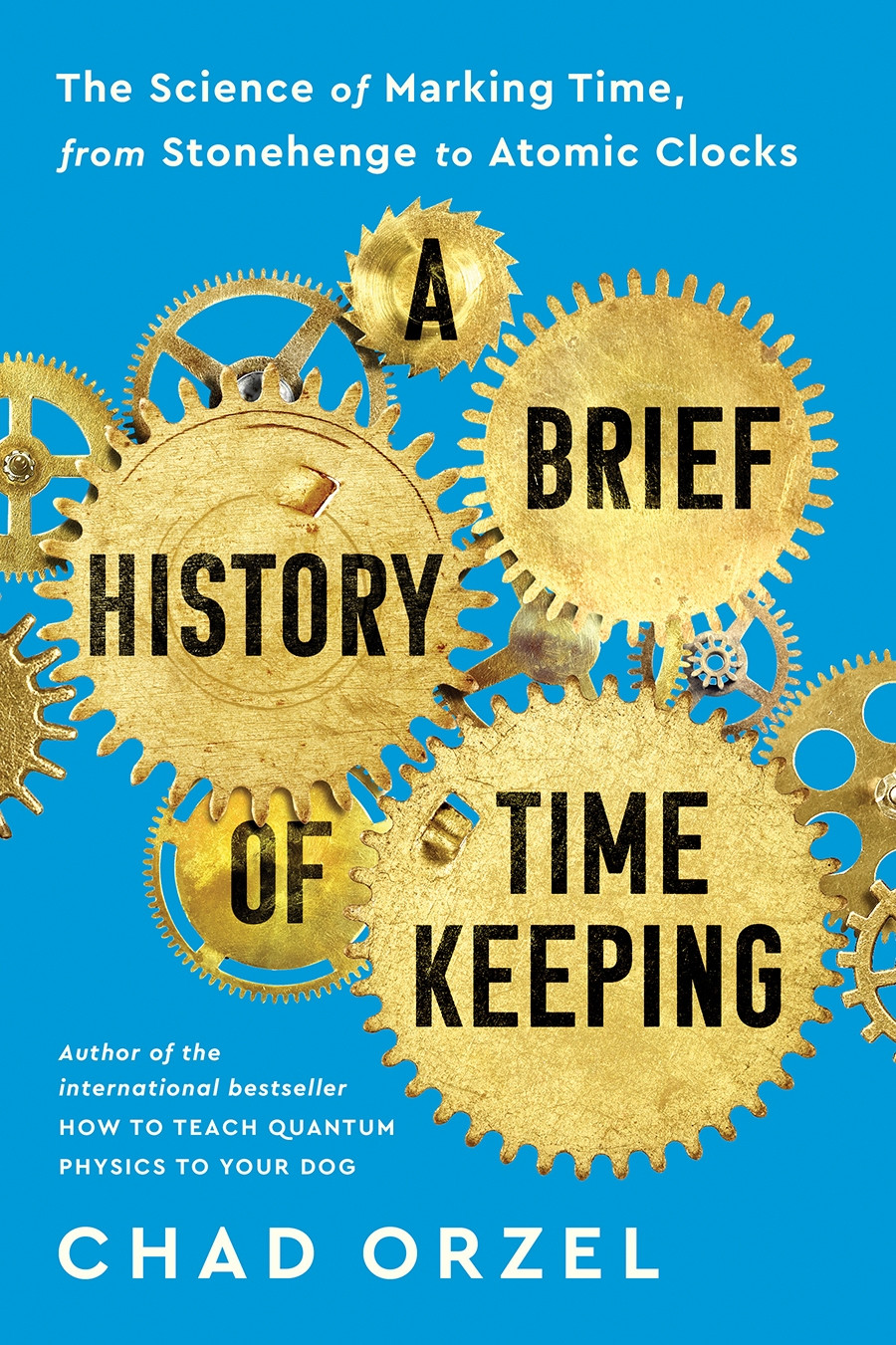
To create a self-managed team, the first step is to establish clear goals. For the team to track its progress, you should set clear metrics. You might be able to lead the industry's net promoter scores. If the self-managed team is new, you may have to hire new members to ensure success. To ensure that employees are able to understand the changes, it is a good idea to train them.
FAQ
Why is it so important for companies that they use project management techniques
Project management techniques can be used to ensure smooth project execution and meeting deadlines.
This is due to the fact that most businesses rely heavily upon project work in order to produce goods, and services.
Companies need to manage these projects efficiently and effectively.
Companies that do not manage their projects effectively risk losing time, money, or reputation.
Why is it so hard to make smart business decisions?
Businesses are complex systems, and they have many moving parts. Their leaders must manage multiple priorities, as well as dealing with uncertainty.
To make good decisions, you must understand how these factors affect the entire system.
You must first consider what each piece of the system does and why. You then need to consider how those individual pieces interact with each other.
Ask yourself if there are hidden assumptions that have influenced your behavior. If so, it might be worth reexamining them.
You can always ask someone for help if you still have questions after all of this. You may be able to see things from a different perspective than you are and gain insight that can help you find a solution.
How does a manager learn to manage?
Through demonstrating good management skills at every opportunity
Managers must constantly monitor the performance of their subordinates.
You must act quickly if you notice that your subordinate isn’t performing to their standards.
It is important to be able identify areas that need improvement and what can be done to improve them.
What does the term "project management” mean?
This refers to managing all activities that are involved in a project's execution.
We include defining the scope of the project, identifying the requirements, preparing the budget, organizing the project team, scheduling the work, monitoring progress, evaluating results, and closing down the project.
What is Six Sigma?
It is a way to improve quality that places emphasis on customer service and continuous learning. The goal is to eradicate defects through statistical techniques.
Six Sigma was developed at Motorola in 1986 as part of its efforts to improve manufacturing processes.
This idea quickly spread throughout the industry. Today, many organizations use six sigma methods for product design, production and delivery.
Statistics
- Our program is 100% engineered for your success. (online.uc.edu)
- As of 2020, personal bankers or tellers make an average of $32,620 per year, according to the BLS. (wgu.edu)
- Hire the top business lawyers and save up to 60% on legal fees (upcounsel.com)
- The average salary for financial advisors in 2021 is around $60,000 per year, with the top 10% of the profession making more than $111,000 per year. (wgu.edu)
- UpCounsel accepts only the top 5 percent of lawyers on its site. (upcounsel.com)
External Links
How To
How does Lean Manufacturing work?
Lean Manufacturing uses structured methods to reduce waste, increase efficiency and reduce waste. They were created in Japan by Toyota Motor Corporation during the 1980s. The primary goal was to make products with lower costs and maintain high quality. Lean manufacturing focuses on eliminating unnecessary steps and activities from the production process. It consists of five basic elements: pull systems, continuous improvement, just-in-time, kaizen (continuous change), and 5S. Pull systems allow customers to get exactly what they want without having to do extra work. Continuous improvement involves constantly improving upon existing processes. Just-in-time refers to when components and materials are delivered directly to the point where they are needed. Kaizen means continuous improvement. Kaizen involves making small changes and improving continuously. Five-S stands for sort. It is also the acronym for shine, standardize (standardize), and sustain. These five elements work together to produce the best results.
Lean Production System
Six key concepts underlie the lean production system.
-
Flow is about moving material and information as near as customers can.
-
Value stream mapping - Break down each stage in a process into distinct tasks and create an overview of the whole process.
-
Five S’s - Sorted, In Order. Shine. Standardize. And Sustain.
-
Kanban: Use visual signals such stickers, colored tape, or any other visual cues, to keep track your inventory.
-
Theory of constraints - identify bottlenecks during the process and eliminate them with lean tools like Kanban boards.
-
Just-intime - Order components and materials at your location right on the spot.
-
Continuous improvement - Make incremental improvements rather than overhauling the entire process.