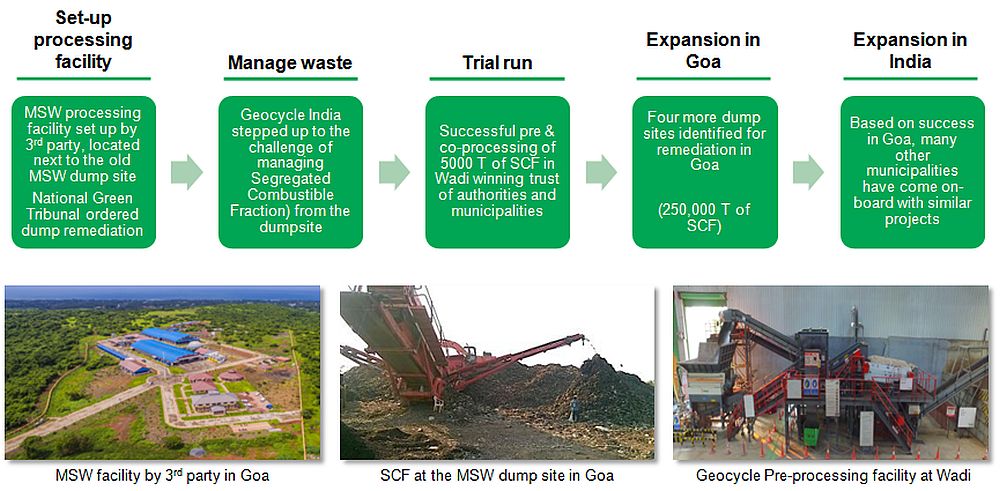
A number of important rules are contained in an ISO document. It is important that abbreviations are clear and precise. Some forms of punctuation must be avoided. These include symbols for quantities or forms of language. These guidelines assist readers in understanding the ISO document as well as its contents.
Forms
Electronic ISO document forms can improve your company's quality process, regulatory compliance, customer satisfaction, and overall business performance. It is important to keep the forms simple and break them up into different data types. Also, ensure that they are part of an overall process. Agile development is key, and it is helpful to gather user requirements early on. User testing can also be useful as it can uncover issues you did not anticipate. Additionally, all users should receive software-specific training.
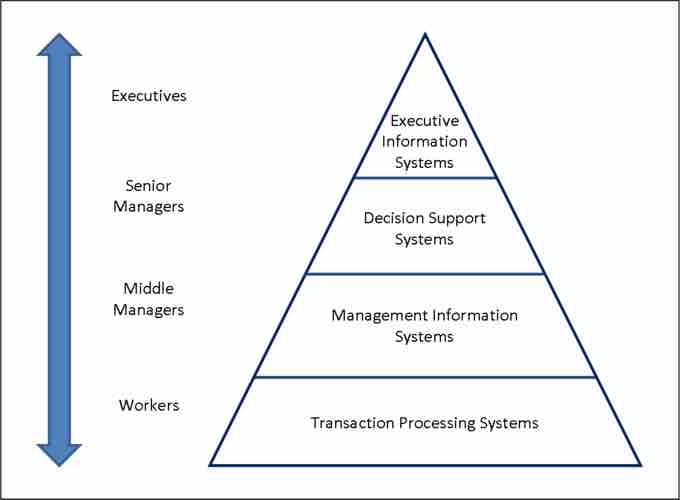
Symbols for quantities
In ISO documents, the symbols are used to indicate quantities. These symbols are usually abbreviated terms, and are generally written in italics, unlike words or numbers that are written in lowercase. Some abbreviations can also have special meanings. For example, 'net current value' or the 'internal rates of return'. The standard also specifies what symbols should be used when referring to quantities.
Acronyms
Most people are familiar with some common acronyms, especially if they read ISO documents regularly. CAR stands for Corrective Activity Request. The Corrective Action Request (CA) is an activity that initiates a Corrective Activity. This involves, in general, investigating a problem and finding its root cause. But, the Corrective Action lifecycle can also be referred to.
Language
Language of ISO document is vital in making sure that the intended audience understands the document. The conventions that are used to define this language are listed below. While abbreviations can be used frequently, the first word must always be capitalized. For example, the abbreviation "ac" for alternating current is acceptable, but "d.c." is not acceptable for radio frequency.
Formatting
Documentation is an important aspect of ISO standards. However, some organizations overdocument, creating an inflexible system. Make sure your documentation adheres to the correct structure.
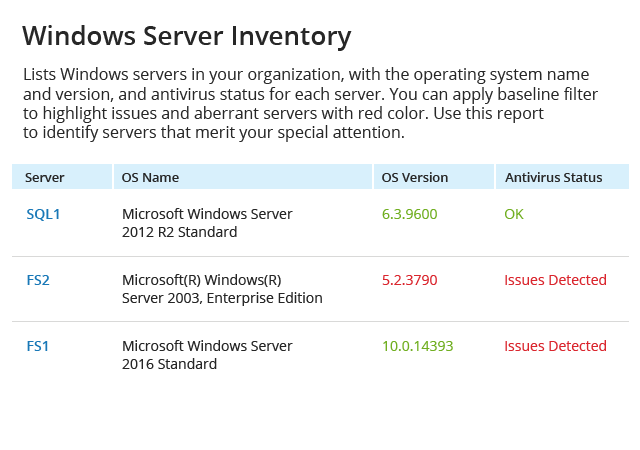
Publishing
ISO publishes documents in different formats. ISO documents are known as IEC standards and ISO standards. They were created by the American Society for Testing and Materials and ISO/IEC JTC 1. The ISO standards may not be the same as ASTM. Some standards are not complete, and they are not published. This means that the publication title often does not include their name.
FAQ
How can we create a successful company culture?
A company culture that values and respects its employees is a successful one.
It is based on three principles:
-
Everybody can contribute something valuable
-
People are treated with respect
-
It is possible to have mutual respect between groups and individuals
These values are evident in the way that people act. For example, they will treat others with courtesy and consideration.
They will listen respectfully to the opinions of others.
These people will inspire others to share thoughts and feelings.
Additionally, the company culture encourages open communication as well as collaboration.
People can freely express their opinions without fear or reprisal.
They understand that errors will be tolerated as long they are corrected honestly.
Finally, the company culture encourages honesty as well as integrity.
Everybody knows they have to tell the truth.
Everyone recognizes that rules and regulations are important to follow.
People don't expect special treatment or favors.
What's the difference between leadership & management?
Leadership is about being a leader. Management is about controlling others.
A leader inspires followers while a manager directs workers.
A leader motivates people to achieve success; a manager keeps workers on task.
A leader develops people; a manager manages people.
What is Six Sigma, exactly?
It's an approach to quality improvement that emphasizes customer service and continuous learning. The objective is to eliminate all defects through statistical methods.
Motorola created Six Sigma as part of their efforts to improve manufacturing processes in 1986.
The idea quickly spread in the industry. Many organizations today use six-sigma methods to improve product design and production, delivery and customer service.
How can a manager enhance his/her leadership skills?
It is important to have good management skills.
Managers must continuously monitor the performance levels of their subordinates.
It is important to take immediate action if your subordinate doesn't perform as expected.
You should be able pinpoint what needs to improve and how to fix it.
Statistics
- Your choice in Step 5 may very likely be the same or similar to the alternative you placed at the top of your list at the end of Step 4. (umassd.edu)
- 100% of the courses are offered online, and no campus visits are required — a big time-saver for you. (online.uc.edu)
- As of 2020, personal bankers or tellers make an average of $32,620 per year, according to the BLS. (wgu.edu)
- The profession is expected to grow 7% by 2028, a bit faster than the national average. (wgu.edu)
- Hire the top business lawyers and save up to 60% on legal fees (upcounsel.com)
External Links
How To
How do you do the Kaizen method?
Kaizen means continuous improvement. This Japanese term refers to the Japanese philosophy of continuous improvement that emphasizes incremental improvements and constant improvement. This is a collaborative process in which people work together to improve their processes continually.
Kaizen is one the most important methods of Lean Manufacturing. This concept requires employees to identify and solve problems during manufacturing before they become major issues. This increases the quality of products and reduces the cost.
Kaizen is a way to raise awareness about what's happening around you. If something is wrong, it should be corrected immediately so that no problem occurs. So, if someone notices a problem while working, he/she should report it to his/her manager.
When doing kaizen, there are some principles we must follow. We always start from the end product and move toward the beginning. In order to improve our factory's production, we must first fix the machines producing the final product. Next, we fix the machines which produce components. Then, we fix those who work directly with the machines.
This approach is called 'kaizen' because it focuses on improving everything steps by step. Once we have finished fixing the factory, we return to the beginning and work until perfection.
Before you can implement kaizen into your business, it is necessary to learn how to measure its effectiveness. There are many ways to tell if kaizen is effective. One of these ways is to check the number of defects found on the finished products. Another way to find out how productive your company has been since you implemented kaizen is to measure the increase in productivity.
You can also find out if kaizen works by asking yourself why you decided to implement it. You were trying to save money or obey the law? Did you really believe that it would be a success factor?
Congratulations! You are ready to start kaizen.