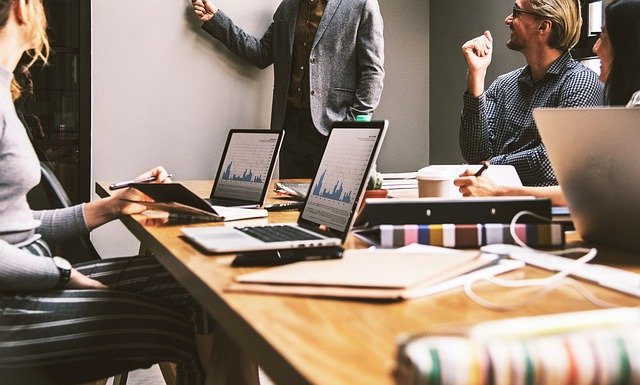
The most important aspect of any building project is its construction management. A construction manager represents the owner's interests and oversees all aspects of the project. His or her responsibility is to make sure the project is completed on-time and within budget. In order to fulfill the owner's needs, he or her also works with the general contractor as well as the architect. A construction manager must be proficient in all aspects of construction techniques and practices to be successful.
Pre-construction
The most important part of construction is the pre-construction management. This involves planning, estimating and managing all aspects of a construction project. It involves working together with all parties to define the design intent, requirements of the end-user, and scope of the project. Final goal is to complete projects on time and within budget.
The client and the partner in construction will work closely together to produce detailed drawings, schedules. budgets. and manpower projections. Regular communication is important during this phase. It helps identify potential construction problems and how they can be resolved. This helps to ensure that the project is on schedule.
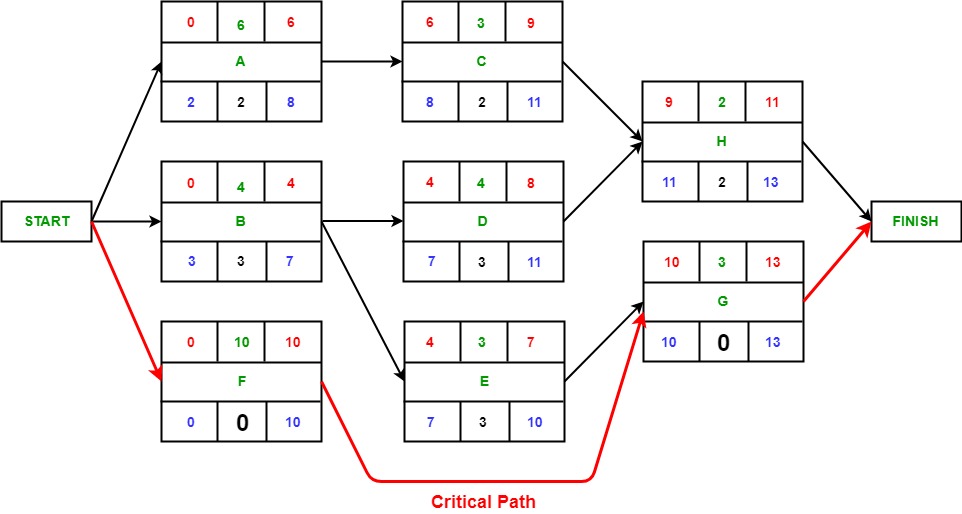
Hiring subcontractors
Construction management is not complete without subcontractors. Subcontractors can play an important role in the overall project, and can significantly increase the project's success. However, subcontractors should be chosen carefully to avoid problems or delays. They must have a proven track record, and a reputation to deliver quality work.
Subcontractors, although they are independent contractors are still protected by the same legal protections that employees. It is therefore important to fully understand the legalities of subcontractors being hired. Subcontractors, being independent contractors, are subject to the same tax obligations that a general contractor. This can make them susceptible to paying back taxes and employee benefits.
Construction project closeout
It is critical for the financial and operation health of an owner to successfully close out a construction job. It is important to plan ahead and coordinate early with all parties. There are several key areas to consider. Following these steps will help to minimize disputes and problems. These are some tips that will help you plan for a successful closing of your project.
The process of closing a construction project can be lengthy. It involves punch lists, final inspections and submission of as-builts. A well-planned and executed closeout can save you time, money, stress, and even headaches. In addition, it will reduce stress for everyone involved, including your clients and employees.
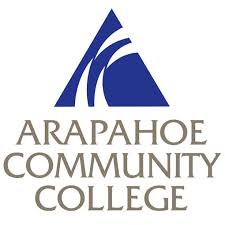
Cloud-based software
Your ROI can be maximized with construction management software. These solutions can be used to automate repetitive tasks as well as integrate with other business software. These apps can be used to monitor and manage budgets and schedules, make changes and get information from subcontractors. Many of these applications are integrated with CRM and takeoff software. You can use them to handle many types of projects.
Another benefit of cloud-based construction management software is the ability to adapt quickly to changing field needs. Cloud-based software gives users instant access to the latest features, and allows them to update their software instantly. No more waiting for updates.
FAQ
Six Sigma is so popular.
Six Sigma is easy and can deliver significant results. It also provides a framework for measuring improvements and helps companies focus on what matters most.
How does Six Sigma function?
Six Sigma uses statistical analyses to locate problems, measure them, analyze root cause, fix problems and learn from the experience.
The first step is identifying the problem.
Next, data is collected and analyzed to identify trends and patterns.
Then corrective actions are taken to solve the problem.
The data are then reanalyzed to see if the problem is solved.
This continues until you solve the problem.
What is Kaizen, exactly?
Kaizen, a Japanese term that means "continuous improvement," is a philosophy that encourages employees and other workers to continuously improve their work environment.
Kaizen is built on the belief that everyone should be able do their jobs well.
How do we build a culture that is successful in our company?
A culture of respect and value within a company is key to a productive culture.
It's based on three main principles:
-
Everybody can contribute something valuable
-
People are treated fairly
-
Individuals and groups can have mutual respect
These values are evident in the way that people act. For example, they will treat others with courtesy and consideration.
They will listen respectfully to the opinions of others.
They encourage others to express their feelings and ideas.
The company culture promotes collaboration and open communication.
People feel safe to voice their opinions without fear of reprisal.
They understand that mistakes can be forgiven as long as they're dealt with honestly.
The company culture promotes honesty, integrity, and fairness.
Everyone knows that they must always tell truth.
Everyone is aware that rules and regulations apply to them.
Nobody expects to be treated differently or given favors.
What are the three main management styles you can use?
The three basic management styles are: authoritarian, laissez-faire, and participative. Each style has its strengths and weaknesses. Which style do YOU prefer? Why?
Autoritarian - The leader sets direction and expects everyone else to follow it. This style is best when the organization has a large and stable workforce.
Laissez-faire - The leader allows each individual to decide for him/herself. This style works best when an organization is small and dynamic.
Participative - Leaders listen to all ideas and suggestions. This style works best in smaller organizations where everyone feels valued.
Statistics
- Hire the top business lawyers and save up to 60% on legal fees (upcounsel.com)
- The profession is expected to grow 7% by 2028, a bit faster than the national average. (wgu.edu)
- This field is expected to grow about 7% by 2028, a bit faster than the national average for job growth. (wgu.edu)
- 100% of the courses are offered online, and no campus visits are required — a big time-saver for you. (online.uc.edu)
- The BLS says that financial services jobs like banking are expected to grow 4% by 2030, about as fast as the national average. (wgu.edu)
External Links
How To
What is Lean Manufacturing?
Lean Manufacturing is a method to reduce waste and increase efficiency using structured methods. They were created in Japan by Toyota Motor Corporation during the 1980s. The main goal was to produce products at lower costs while maintaining quality. Lean manufacturing seeks to eliminate unnecessary steps and activities in the production process. It is made up of five elements: continuous improvement, continuous improvement, just in-time, continuous change, and 5S. Pull systems involve producing only what the customer wants without any extra work. Continuous improvement is constantly improving upon existing processes. Just-in time refers to components and materials being delivered right at the place they are needed. Kaizen means continuous improvement. Kaizen involves making small changes and improving continuously. Last but not least, 5S is for sort. These five elements are used together to ensure the best possible results.
Lean Production System
Six key concepts are the basis of lean production:
-
Flow - focus on moving material and information as close to customers as possible;
-
Value stream mapping- This allows you to break down each step of a process and create a flowchart detailing the entire process.
-
Five S's - Sort, Set In Order, Shine, Standardize, and Sustain;
-
Kanban – visual signals like colored tape, stickers or other visual cues are used to keep track inventory.
-
Theory of constraints: identify bottlenecks in your process and eliminate them using lean tools, such as kanban board.
-
Just-in-time - deliver components and materials directly to the point of use;
-
Continuous improvement - make incremental improvements to the process rather than overhauling it all at once.