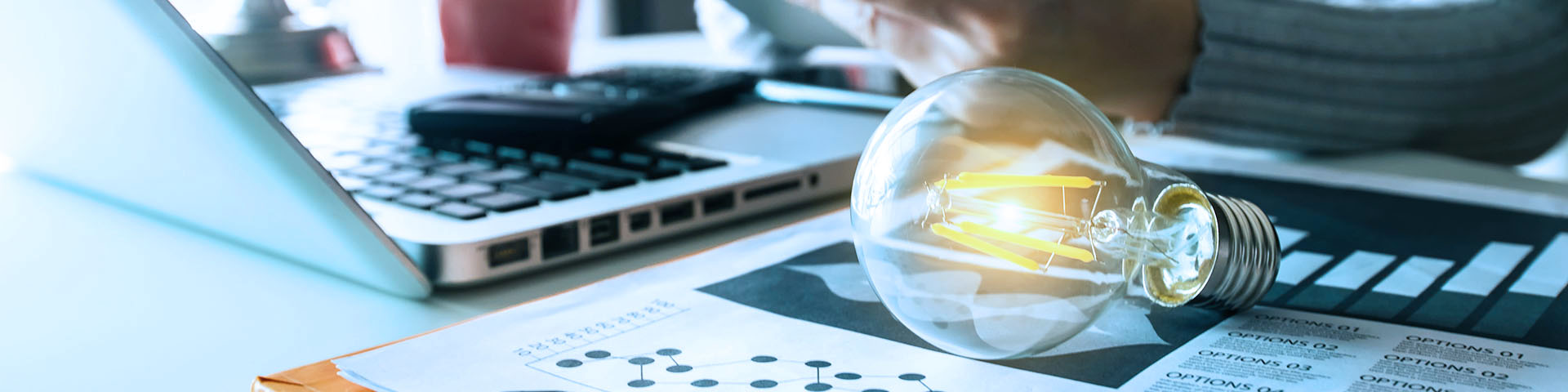
Internships and apprenticeships are well-known, but what about construction mentorships? A construction mentorship is a great idea for a corporate environment. Boeing, an aerospace giant has strong professional development programs. They also emphasize peer mentorship. Even small local construction firms may offer mentorship programs that are modest and not too extensive.
Construction mentors need to be a volunteer association
The construction industry must have a robust mentoring system in order to keep its workers motivated, despite increasing project backlogs. 86% percent of employers in this industry report that they have difficulty filling professional and hourly positions. Arizona alone will need 228,000 craft professionals by 2024. Mentoring is a key aspect of this system, and widespread commitment to this system could revolutionize the entire industry.
High school students who are interested in a career as a construction worker can use the ACE Mentor Program of America. This national non-profit organization employs a network mentors to connect students with real-world opportunities. They also promote the importance of careers in building trades. It also offers scholarship and grant opportunities. A second important resource is The National Association of Women in Construction. This association prioritizes mentorship and offers a robust volunteer mentorship program. This association also publishes guidelines for mentors.
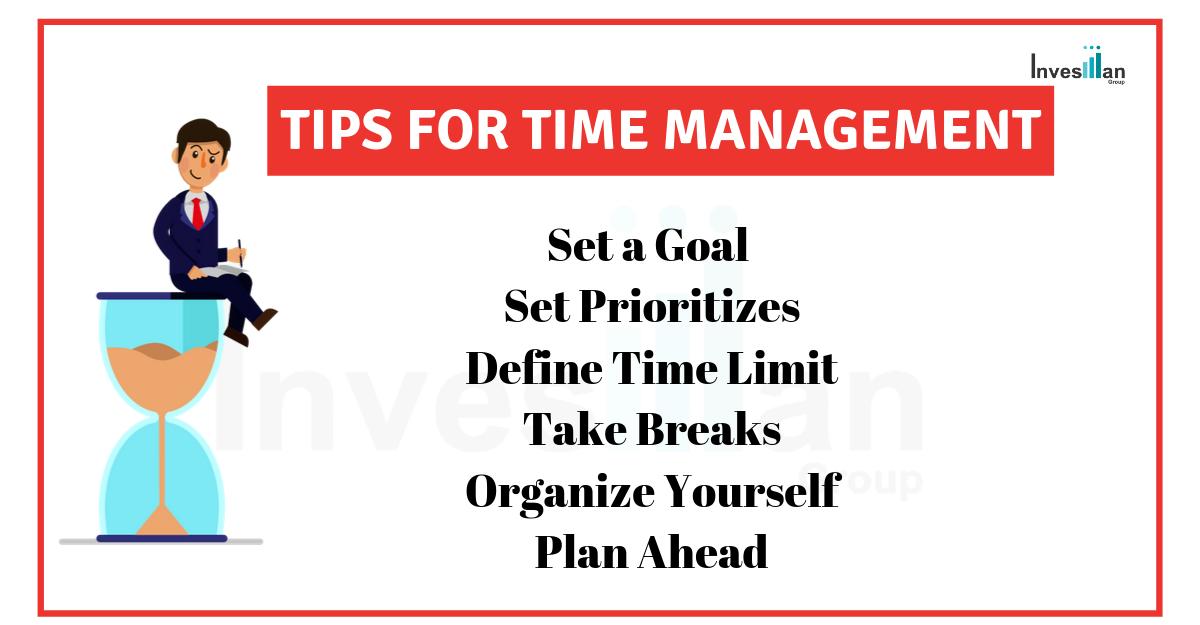
Importance of construction mentorship
Mentorship is an important way to develop future workers. It can promote a culture and develop strong young professionals within a company. Mentors can pass along their knowledge and experiences to new mentees, who in turn can pass them on to the next generation. Construction companies can foster a culture that mentors to help them build the next generation of industry leaders.
Mentors can boost confidence and help people secure lucrative opportunities. Regular contact with experienced colleagues can help to reorient efforts, clarify career goals, and provide valuable support. A widespread commitment to construction mentorship could have a significant positive impact on the entire construction industry.
Young talent can get the job of their dreams by being mentored in the construction industry. Mentors are able to teach apprentices how they can use machines and systems as well how to deal effectively with clients. Ultimately, successful internships can lead to full-time employment for the mentee after graduation.
Rules for registration as construction mentors
The South African Council for Project and Construction Management Professions has published new registration rules for Construction Mentors. These rules were revised to simplify the registration process for anyone interested in this profession. A small number of individuals have applied to become Professional Construction Mentors. This category is intended to attract people with industry experience and skills.
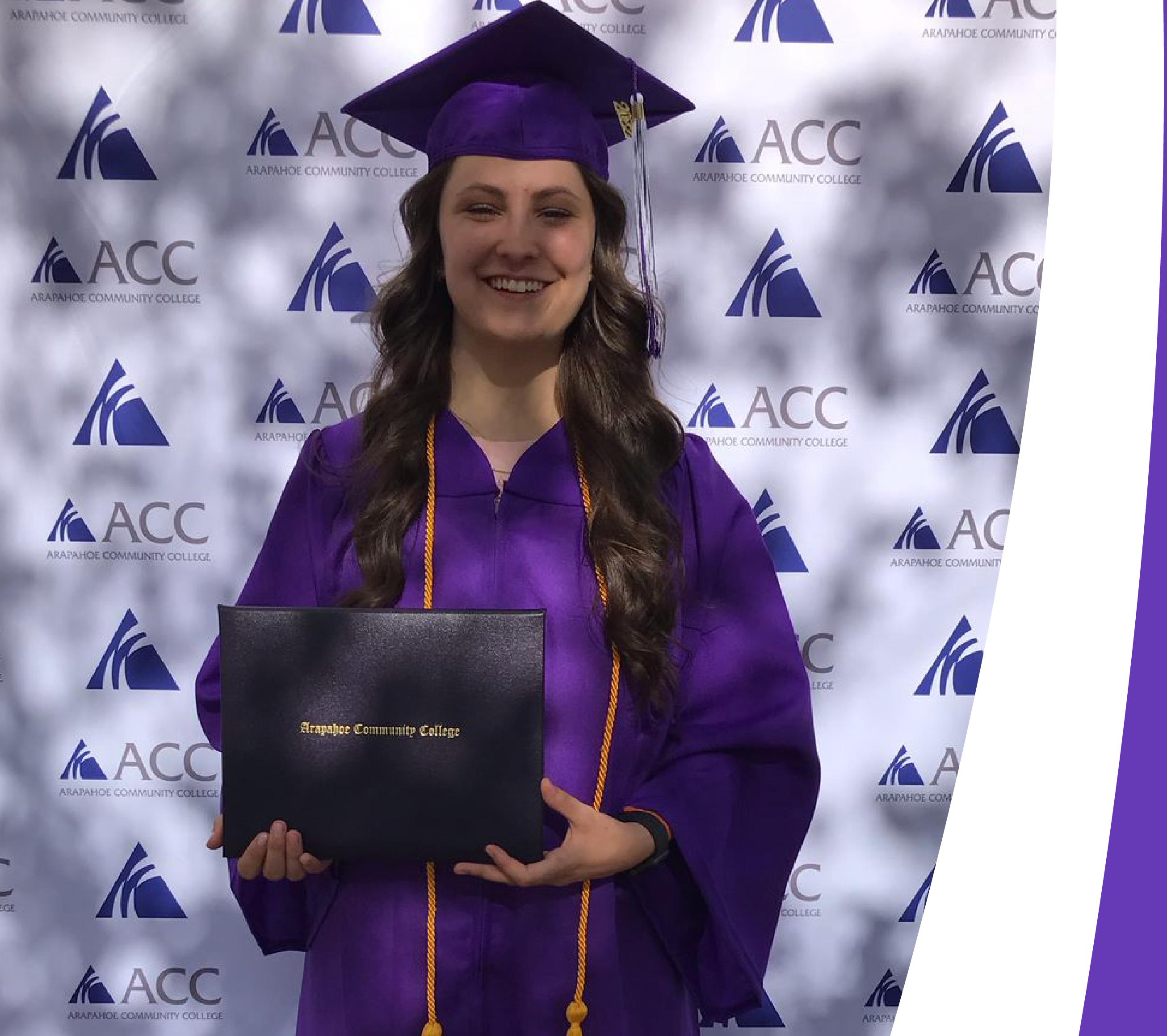
Being a mentor in construction has many benefits. These include increased job opportunities as well as business development opportunities. But, it is not certain that being a mentor will increase your job prospects. You should carefully read the rules for becoming a mentor. Although mentoring is not guaranteed to land you a job in the future, it can be a great way to get started in your career.
FAQ
What is a management tool to help with decision-making?
A decision matrix, a simple yet powerful tool for managers to make decisions, is the best. They can think about all options and make informed decisions.
A decision matrix can be used to show alternative options as rows or columns. It is easy to see how each option affects the other options.
We have four options in this example. They are represented by the boxes to the left of the matrix. Each box represents an option. The top row represents the current state of affairs, and the bottom row is indicative of what would happen in the event that nothing were done.
The middle column displays the impact of selecting Option 1. It would translate into an increase in sales from $2million to $3million.
These are the results of selecting Options 2 or 3. These are good changes, they increase sales by $1million or $500,000. These changes can also have negative effects. Option 2 increases the cost of goods by $100,000. Option 3 decreases profits and makes them less attractive by $200,000.
The final column shows the results for Option 4. This would result in a reduction of sales of $1 million.
The best thing about a decision matrix is the fact that you don't have to remember which numbers go with what. Simply look at the cells to instantly determine if one choice is better than the other.
This is because the matrix has done all the hard work. It's as easy as comparing numbers in the appropriate cells.
Here's an example showing how you might use a Decision Matrix in your business.
You need to decide whether to invest in advertising. You'll be able increase your monthly revenue by $5000 if you do. You'll also have additional expenses up to $10,000.
Look at the cell immediately below the one that states "Advertising" to calculate the net investment in advertising. It's $15,000. Advertising is a worthwhile investment because it has a higher return than the costs.
It seems so difficult sometimes to make sound business decisions.
Complex systems and many moving parts make up businesses. People who manage them have to balance multiple priorities while dealing with complexity and uncertainty.
To make good decisions, you must understand how these factors affect the entire system.
It is important to consider the functions and reasons for each part of the system. It is important to then consider how the individual pieces relate to each other.
You need to ask yourself if your previous actions have led you to make unfounded assumptions. If you don't have any, it may be time to revisit them.
You can always ask someone for help if you still have questions after all of this. You may be able to see things from a different perspective than you are and gain insight that can help you find a solution.
How does a manager motivate his/her employees?
Motivation is the desire for success.
Engaging in something fun can be a great way to get motivated.
Another way to get motivated is to see yourself as a contributor to the success of the company.
For example: If you want to be a doctor, you might find it more motivating seeing patients than reading medical books all day.
Another type of motivation comes from within.
You may feel strongly that you are responsible to help others.
Perhaps you enjoy working hard.
If you don’t feel motivated, find out why.
Then try to think about ways to change your situation to be more motivated.
What is the difference between TQM and Six Sigma?
The main difference between these two quality-management tools is that six-sigma concentrates on eliminating defects while total QM (TQM), focuses upon improving processes and reducing expenses.
Six Sigma is a methodology for continuous improvement. It emphasizes the elimination and improvement of defects using statistical methods, such as control charts, P-charts and Pareto analysis.
This method aims to reduce variation in product production. This is achieved by identifying and addressing the root causes of problems.
Total quality management involves measuring and monitoring all aspects of the organization. It also involves training employees to improve performance.
It is used to increase productivity.
What are the 5 management processes?
Planning, execution, monitoring and review are the five stages of any business.
Setting goals for the future is part of planning. Planning includes setting goals for the future.
Execution takes place when you actually implement the plans. It is important to ensure that everyone follows the plans.
Monitoring is the process of evaluating your progress toward achieving your objectives. This should involve regular reviews of performance against targets and budgets.
Each year, reviews are held at the end. These reviews allow you to evaluate whether the year was successful. If not, then it may be possible to make adjustments in order to improve performance next time.
After each year's review, evaluation occurs. It helps you identify the successes and failures. It also gives feedback on how well people did.
What is TQM, exactly?
The industrial revolution led to the birth and growth of the quality movement. Manufacturing companies realized they couldn't compete solely on price. They needed to improve quality and efficiency if they were going to remain competitive.
Management developed Total Quality Management to address the need for improvement. It focused on all aspects of an organisation's performance. It included continuous improvement processes, employee involvement, and customer satisfaction.
What's the difference between leadership & management?
Leadership is about influence. Management is about controlling others.
A leader inspires his followers while a manager directs the workers.
A leader motivates people to achieve success; a manager keeps workers on task.
A leader develops people; a manager manages people.
Statistics
- The BLS says that financial services jobs like banking are expected to grow 4% by 2030, about as fast as the national average. (wgu.edu)
- As of 2020, personal bankers or tellers make an average of $32,620 per year, according to the BLS. (wgu.edu)
- The average salary for financial advisors in 2021 is around $60,000 per year, with the top 10% of the profession making more than $111,000 per year. (wgu.edu)
- Your choice in Step 5 may very likely be the same or similar to the alternative you placed at the top of your list at the end of Step 4. (umassd.edu)
- Hire the top business lawyers and save up to 60% on legal fees (upcounsel.com)
External Links
How To
How can Lean Manufacturing be done?
Lean Manufacturing processes are used to reduce waste and improve efficiency through structured methods. They were created in Japan by Toyota Motor Corporation during the 1980s. The goal was to produce quality products at lower cost. Lean manufacturing is about eliminating redundant steps and activities from the manufacturing process. It has five components: continuous improvement and pull systems; just-in time; continuous change; and kaizen (continuous innovation). Pull systems are able to produce exactly what the customer requires without extra work. Continuous improvement involves constantly improving upon existing processes. Just-in-time refers to when components and materials are delivered directly to the point where they are needed. Kaizen is continuous improvement. This can be achieved by making small, incremental changes every day. Last but not least, 5S is for sort. These five elements work together to produce the best results.
The Lean Production System
Six key concepts are the basis of lean production:
-
Flow - The focus is on moving information and material as close as possible to customers.
-
Value stream mapping is the ability to divide a process into smaller tasks, and then create a flowchart that shows the entire process.
-
Five S's: Sort, Shine Standardize, Sustain, Set In Order, Shine and Shine
-
Kanban is a visual system that uses visual cues like stickers, colored tape or stickers to keep track and monitor inventory.
-
Theory of constraints - identify bottlenecks during the process and eliminate them with lean tools like Kanban boards.
-
Just-in-time - deliver components and materials directly to the point of use;
-
Continuous improvement - incremental improvements are made to the process, not a complete overhaul.