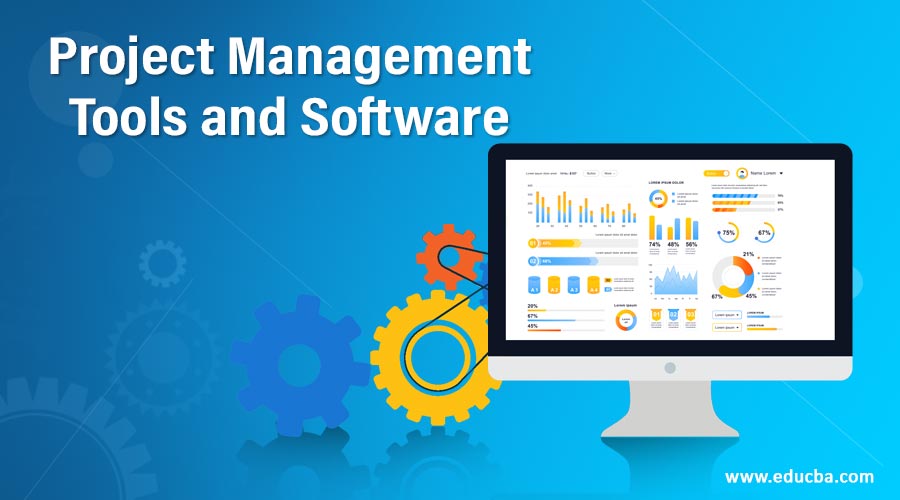
Modern HR practices are essential in today's fast-paced world. This means keeping pace with the expectations of all stakeholders and staying ahead of technologies. A variety of principles can be applied to HR departments to improve their performance. Here are some examples.
Employee orientation
Employee orientation can help new employees feel welcomed and ready for their new role. This orientation can also be a way to reduce turnover. New employees are taught about the company policies and procedures during orientation. This can facilitate a smoother transition to the company. It is important to communicate clearly what the expectations are. A formal and engaging orientation is important for new employees. It helps to reduce turnover.
Performance management
High-performing companies can be created using performance management principles. This is a continuous effort to align employees' efforts and the firm's goals. It is crucial to set clear objectives and criteria. Employees should also be given feedback so they can stay on the right track. It can also reduce costs, increase productivity, improve company performance, and help to lower overall costs.
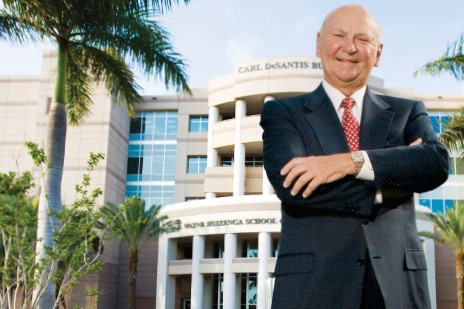
Succession planning
Succession planning can be a process that will help you to develop new leaders in your company. It starts by identifying the gaps in knowledge and skills within your team. Once you have identified these gaps, you can create a learning strategy to fill them. It's also important to have regular performance review meetings and communicate these areas with others.
Integration
Human resource management involves the maximization of scarce resources. This discipline is designed to maximize an organization's effectiveness in using its human capital and increase its productivity. For example, in recent years, the construction industry has suffered from a severe shortage of skilled labor. This shortage is predicted to triple over the next decade, which will impact the productivity of the entire sector.
Staffing levels
Staffing levels are a key component of human resource management. It is essential to have the right staff for the job. Managers need to discuss their staffing needs and determine the optimal level of staff. Not only does it improve customer experience but it can also give companies a better chance of success and growth.
Objectivity
Managers should not be biased or favoritism according to the objective management principle. A manager shouldn't have any preference for one employee over another. Objectivity is crucial to preventing workplace conflicts.
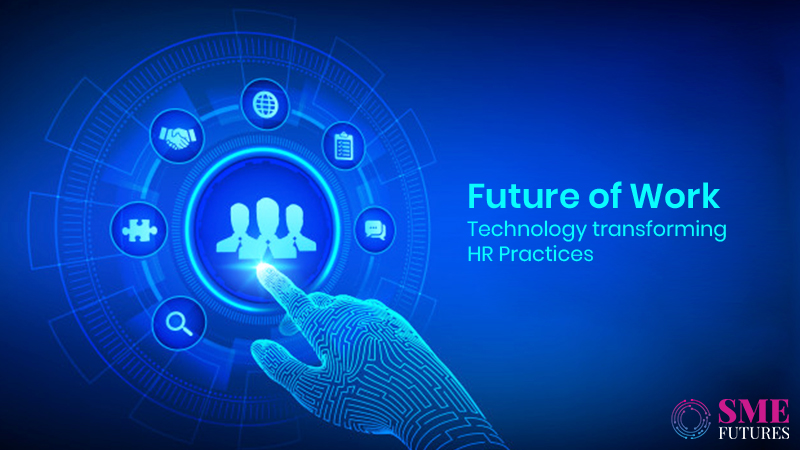
Non-monetary incentives
Non-monetary rewards are an important part of employee retention and engagement strategies. While they are more affordable than monetary rewards, they can still have the same impact. Non-monetary rewards encourage interaction between employees, foster positive feedback and provide opportunities for employees to grow within the company. These rewards are more appealing to employees who come from millennial and gen-Z backgrounds. They tend to value these types more than monetary compensation.
FAQ
What are the 4 main functions of management?
Management is responsible for planning, organizing, directing, and controlling people and resources. Management also involves setting goals and developing policies.
Management assists an organization in achieving its goals by providing direction, coordination and control, leadership, motivation, supervision and training, as well as evaluation.
The following are the four core functions of management
Planning - Planning refers to deciding what is needed.
Organizing - Organization involves deciding what should be done.
Directing – This means to get people to follow directions.
Controlling – Controlling is the process of ensuring that tasks are completed according to plan.
What is Kaizen?
Kaizen, a Japanese term that means "continuous improvement," is a philosophy that encourages employees and other workers to continuously improve their work environment.
Kaizen is built on the belief that everyone should be able do their jobs well.
What are the five management methods?
Planning, execution, monitoring and review are the five stages of any business.
Planning involves setting goals for the future. This includes setting goals for the future and defining what you want.
Execution takes place when you actually implement the plans. It is important to ensure that everyone follows the plans.
Monitoring is the process of evaluating your progress toward achieving your objectives. Regular reviews should be done of your performance against targets or budgets.
Every year, there are reviews. These reviews allow you to evaluate whether the year was successful. If not, then it may be possible to make adjustments in order to improve performance next time.
After the annual review is complete, evaluations are conducted. It helps identify what worked well and what didn't. It provides feedback about how people perform.
Six Sigma is so beloved.
Six Sigma is easy to use and can lead to significant improvements. Six Sigma also gives companies a framework for measuring improvement and helps them focus on what is most important.
Why is it important for companies to use project management techniques?
Project management techniques are used in order to ensure projects run smoothly, and that deadlines are met.
This is because most businesses rely on project work for their products and services.
These projects are essential for companies.
Companies that do not manage their projects effectively risk losing time, money, or reputation.
What is Six Sigma, exactly?
It's a method for quality improvement that focuses on customer service as well as continuous learning. It is a method that eliminates defects using statistical techniques.
Motorola developed Six Sigma in 1986 to help improve its manufacturing processes.
The idea quickly spread in the industry. Many organizations today use six-sigma methods to improve product design and production, delivery and customer service.
Statistics
- As of 2020, personal bankers or tellers make an average of $32,620 per year, according to the BLS. (wgu.edu)
- Our program is 100% engineered for your success. (online.uc.edu)
- Hire the top business lawyers and save up to 60% on legal fees (upcounsel.com)
- Your choice in Step 5 may very likely be the same or similar to the alternative you placed at the top of your list at the end of Step 4. (umassd.edu)
- This field is expected to grow about 7% by 2028, a bit faster than the national average for job growth. (wgu.edu)
External Links
How To
How can Lean Manufacturing be done?
Lean Manufacturing methods are used to reduce waste through structured processes. They were created by Toyota Motor Corporation in Japan in the 1980s. The primary goal was to make products with lower costs and maintain high quality. Lean manufacturing emphasizes removing unnecessary steps from the production process. It includes five main elements: pull systems (continuous improvement), continuous improvement (just-in-time), kaizen (5S), and continuous change (continuous changes). Pull systems are able to produce exactly what the customer requires without extra work. Continuous improvement is the continuous improvement of existing processes. Just-in-time is when components and other materials are delivered at their destination in a timely manner. Kaizen stands for continuous improvement. Kaizen can be described as a process of making small improvements continuously. Fifth, the 5S stand for sort, set up in order to shine, standardize, maintain, and standardize. To achieve the best results, these five elements must be used together.
Lean Production System
Six key concepts are the basis of lean production:
-
Flow - The focus is on moving information and material as close as possible to customers.
-
Value stream mapping - Break down each stage in a process into distinct tasks and create an overview of the whole process.
-
Five S's: Sort, Shine Standardize, Sustain, Set In Order, Shine and Shine
-
Kanban - visual cues such as stickers or colored tape can be used to track inventory.
-
Theory of constraints: identify bottlenecks in your process and eliminate them using lean tools, such as kanban board.
-
Just-in time - Get components and materials delivered right at the point of usage;
-
Continuous improvement: Make incremental improvements to the process instead of overhauling it completely.