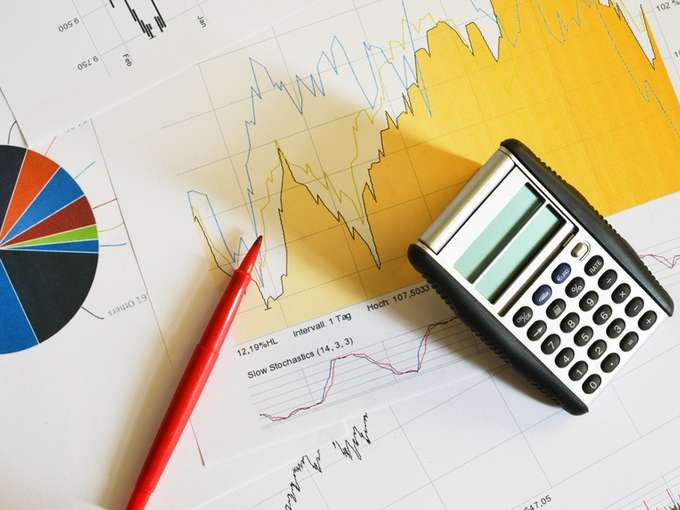
Organic waste disposal can be complicated, especially for businesses and offices with limited space. It is important to review your policies and procedures regarding organic waste disposal before you are faced with them. This includes yard trimmings. Untreated wood, untreated timber, pulled or pulled weeds, as well toothpicks. Anaerobic digestion and biosolids can also be used to decompose organic material.
Anaerobic digestion
Anaerobic digestion is a biological process which can treat a variety organic wastes. It can also produce low-cost biogas. Anaerobic digestion is more environmentally friendly than landfilling because it can extract nutrients from organic matter that it is processing. Anaerobic digestion is a great tool for agriculture and the environment.
New York City and EPA have both set ambitious targets to reduce organic waste. Both cities want to eliminate all organic waste by 2030. New York City's Zero Waste program has been in full swing and now includes curbside organic waste pickup and drop-off.
Co-digestion
Co-digestion is an organic waste disposal method that takes advantage of existing expertise and infrastructure. The process recycles food waste, which in turn reduces greenhouse gases emissions. This process can be used to reduce costs as well as offer diversion opportunities. Co-digestion can be a feasible alternative for urban and agricultural waste management, as it can create a valuable product.
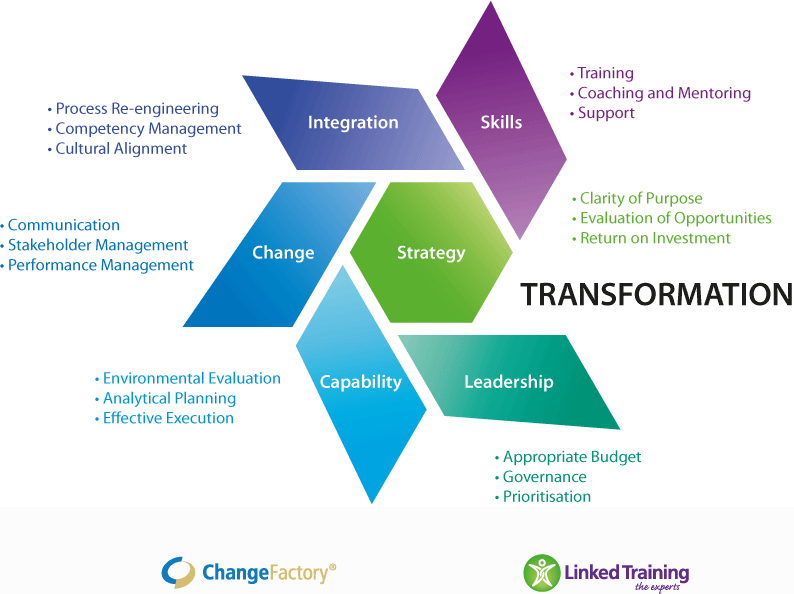
Researchers discovered that the levels of microbial communities in both types digesters were significantly greater than those found in food waste. Firmicutes (Chloroflexi), Bacteroidetes and Actinobacteria were major bacteria found in both types. The distribution of these bacteria was not uniform. In MDi, Chloroflexi represented a significant portion of sequences, whereas Bacteroidetes and Actinobacteria had lower proportions.
Composting
The soil can be fertilized and improved by composting organic waste. This process is a key component in the development of a sustainable and healthy environment. This process can also lower the cost of compounding livestock feed, and it can be used to combat global poverty and malnutrition.
While early publications focused mainly on Western European and North American countries, Asian countries have significantly contributed to the body of research on the process. In developing countries, co-composting has contributed to modernising waste management practices.
Biosolids
Biosolids are soil-based organic materials for waste disposal. These organic waste disposal materials can contain pathogens. Some of these organisms have been found to be harmful to human health. Biosolids can support bacteria and viruses that cause illness such as respiratory infections or diarrhea. The topography and type of soil can affect how long a pathogen survives in biosolids. Different pathogens may be more vulnerable to soil migration than others. It is not known if biosolids or groundwater pollution have an inverse relationship.
The Environmental Protection Agency (EPA) has set regulations on the management of biosolids. These regulations are listed in 40 CFR Section 503 and cover many aspects regarding biosolids disposition. You can either apply biosolids directly to the soil, or compost them. Both methods are beneficial for the soil. The process of composting requires a controlled temperature and oxygen levels to break down the organic waste in biosolids.
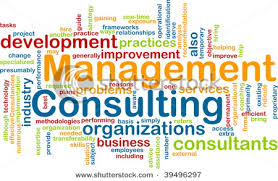
Food processing scrap
There are many options available for food processing waste disposal. You have two options: businesses can either recycle the waste on-site, or hire a hauler to compost their leftovers. Organic materials such as food scraps, food oil, waxed, paper, plants and wood scraps are all acceptable for composting. Different processing systems can accept different types of organic waste.
There are many nutrients and organic compounds in food processing waste. They also contain high biochemical oxygen demands and are prone to biological instability. They must be properly treated to prevent contamination of receiving waters and disruptions to public treatment facilities. The treatment and disposal of food processing wastes is regulated by effluent guidelines and National Pollutant Discharge Elimination System permits.
FAQ
What are some common mistakes managers make?
Sometimes managers make their job harder than they need to.
They may not be able to delegate enough responsibility to staff or provide adequate support.
Managers often lack the communication skills necessary to motivate and guide their teams.
Some managers create unrealistic expectations for their teams.
Managers may prefer to solve every problem for themselves than to delegate responsibility.
What is the difference in leadership and management?
Leadership is about inspiring others. Management is all about controlling others.
A leader inspires followers while a manager directs workers.
Leaders motivate people to succeed; managers keep workers on track.
A leader develops people; a manager manages people.
What's the difference between a program and a project?
A project is temporary; a program is permanent.
A project usually has a specific goal and deadline.
This is often done by a group of people who report to one another.
A program will usually have a set number of goals and objectives.
It is often done by one person.
What are the main styles of management?
The three major management styles are authoritarian (left-faire), participative and laissez -faire. Each style has its strengths and weaknesses. Which style do you prefer? Why?
Authoritarian - The leader sets the direction and expects everyone to comply with it. This style works best if the organization is large and stable.
Laissez-faire - The leader allows each individual to decide for him/herself. This approach works best in small, dynamic organizations.
Participative – The leader listens and takes in ideas from all. This style is most effective in smaller organizations, where everyone feels valued.
What is a management tool to help with decision-making?
A decision matrix can be a simple, but effective tool to assist managers in making decisions. It helps them think systematically about all the options available to them.
A decision matrix represents alternatives in rows and columns. This makes it easy to see how each alternative affects other choices.
In this example, there are four possible options represented by boxes on the left-hand side of the matrix. Each box represents an option. The top row displays the current situation, and the bottom row shows what might happen if nothing is done.
The middle column displays the impact of selecting Option 1. It would translate into an increase in sales from $2million to $3million.
The effects of options 2 and 3 are shown in the next columns. These positive changes can increase sales by $1 million or $500,000. However, these also involve negative consequences. Option 2 increases the cost of goods by $100,000. Option 3 decreases profits and makes them less attractive by $200,000.
Finally, the last column shows the results of choosing Option 4. This results in a decrease of sales by $1,000,000
A decision matrix has the advantage that you don’t have to remember where numbers belong. The best thing about a decision matrix is that you can simply look at the cells, and immediately know whether one option is better or not.
This is because the matrix has already taken care of the hard work for you. It is as simple as comparing the numbers within the relevant cells.
Here's a sample of how you might use decision matrixes in your business.
Decide whether you want to invest more in advertising. If you do this, you will be able to increase revenue by $5000 per month. You will still have to pay $10000 per month in additional expenses.
You can calculate the net result of investing in advertising by looking at the cell directly below the one that says "Advertising." That number is $15 thousand. Advertising is worth more than its cost.
How do you manage your employees effectively?
Achieving employee happiness and productivity is key to managing them effectively.
It also means having clear expectations of their behavior and keeping track of their performance.
Managers need clear goals to be able to accomplish this.
They should communicate clearly with employees. They must communicate clearly with staff members.
They will also need to keep records about their team's activities. These include:
-
What was the result?
-
What was the work involved?
-
Who did it, anyway?
-
Was it done?
-
Why it was done?
This data can be used to evaluate and monitor performance.
What is the main difference between Six Sigma Six Sigma TQM and Six Sigma Six Sigma?
The main difference in these two quality management tools lies in the fact that six sigma is focused on eliminating defects and total quality management (TQM), emphasizes improving processes and reducing costs.
Six Sigma is a methodology for continuous improvement. It emphasizes the elimination or minimization of defects through statistical methods such control charts and p charts.
This method has the goal to reduce variation of product output. This is done by identifying root causes and rectifying them.
Total quality management includes monitoring and measuring all aspects of an organization's performance. Training employees is also part of total quality management.
It is often used to increase productivity.
Statistics
- The average salary for financial advisors in 2021 is around $60,000 per year, with the top 10% of the profession making more than $111,000 per year. (wgu.edu)
- As of 2020, personal bankers or tellers make an average of $32,620 per year, according to the BLS. (wgu.edu)
- This field is expected to grow about 7% by 2028, a bit faster than the national average for job growth. (wgu.edu)
- Your choice in Step 5 may very likely be the same or similar to the alternative you placed at the top of your list at the end of Step 4. (umassd.edu)
- The BLS says that financial services jobs like banking are expected to grow 4% by 2030, about as fast as the national average. (wgu.edu)
External Links
How To
How can you implement the Kaizen technique?
Kaizen means continuous improvement. This Japanese term refers to the Japanese philosophy of continuous improvement that emphasizes incremental improvements and constant improvement. It's a process where people work together to improve their processes continuously.
Kaizen is one the most important methods of Lean Manufacturing. This concept requires employees to identify and solve problems during manufacturing before they become major issues. This improves the quality of products, while reducing the cost.
Kaizen is an approach to making every worker aware and alert to what is happening around them. If something is wrong, it should be corrected immediately so that no problem occurs. If someone spots a problem while at work, they should immediately report it to their manager.
When doing kaizen, there are some principles we must follow. Always start with the end product in mind and work our way back to the beginning. In order to improve our factory's production, we must first fix the machines producing the final product. Next, we repair the machines that make components. Then, the machines that make raw materials. Then we fix the workers, who directly work with these machines.
This is known as "kaizen", because it emphasizes improving each step. After we're done with the factory, it's time to go back and fix the problem.
How to measure kaizen's effectiveness in your business is essential to implement it. There are many ways you can determine if kaizen has been implemented well. One method is to inspect the finished products for defects. Another way is to see how much productivity has increased since implementing kaizen.
Another way to know whether kaizen is working is to ask yourself why did you decide to implement kaizen. Was it just because it was the law or because you wanted to save money? You really believed it would make you successful?
Congratulations! You're now ready to get started with kaizen.