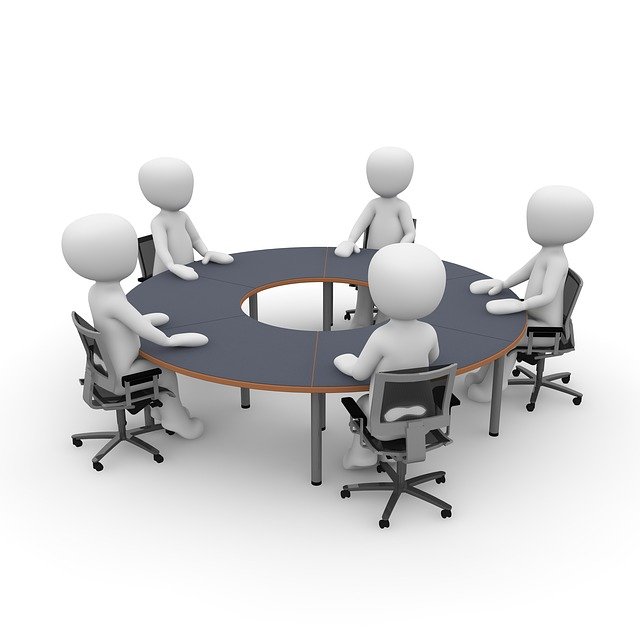
It can boost your professional credibility. It demonstrates that you are knowledgeable of Agile methods and have a sophisticated skill set. You are also up-to-date on market changes. Working professionals need to be flexible and agile in this fast-paced world. Professionals can learn new ways to improve their fields through agile certifications. This allows them excel in their job. This article will highlight some of the benefits associated with becoming an Agile certified professional.
ICAgile's agile certification
ICAgile's agility certification is a competency based certificate. It rewards those who can apply the principles and practices of agile development to solve business issues. The ICAgile Certified Expert credential represents the first step towards an agile career. Individuals who have completed at least one of the four learning tracks and are competent in all four tracks will be awarded this credential. The ICP is a requirement for the ICAgile Certified Expert certificate.
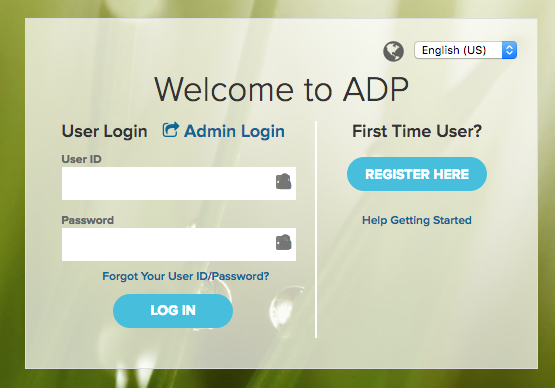
ICAgile is a non-profit organization that promotes Agile practices and guides organizations to establish a culture of continuous improvements. ICAgile has a large number of certified training providers around the world. The courses follow the ICAgile Learning Outcomes and are aligned with the ICAgile certification. ICAgile also works closely with agile practitioners to ensure that training providers comply with the Agile certification program standards.
The Scrum Alliance certification
The Scrum Alliance is an association that supports organizations in adopting agile methodologies. It also provides training and resources for members. The Scrum Alliance was founded by Mike Cohn in 2001, Ken Schwaber, Esther Derby, and has more seventy-five thousands members worldwide. The Alliance sponsors many community groups, both locally and online. Visit their website for more information on the Scrum Alliance certification program.
Certified Scrum Product Owner (CSPPO), certification is for Scrum professionals that work on the "business sides" of projects. As a CSP-PO, you will learn how to adopt agile while also working to meet the needs of the customer. A course must be completed in order to become a CSPPO. For this certification you will need at least 24 month of product ownership experience.
The PMI's Agile Certified Practitioner certification
PMI-ACP is a PMI certification that recognizes those who have experience in agile project management. To qualify for the ACP, applicants must have completed 21 hours of training on Agile methods, which must cover the material in the PMI-ACP exam. PMI will also accept applicants with equivalent credentials. ACP applicants must have at least three years of project management experience. This certification is the most sought-after among PMI's other certifications.
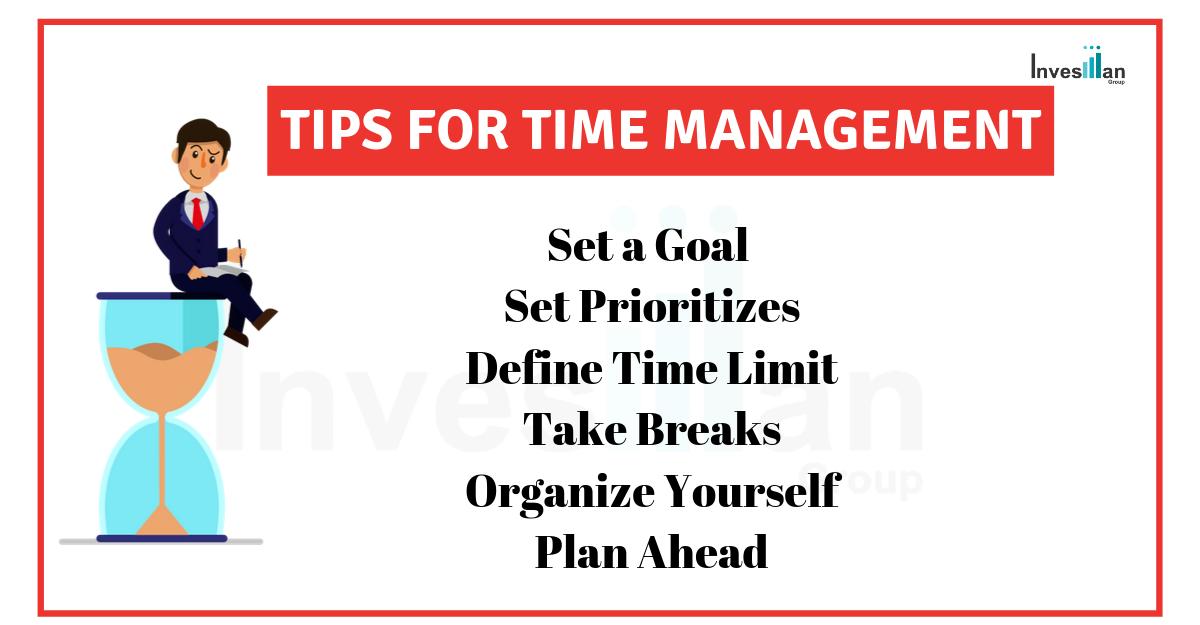
ACP exam contains 120 multiple-choice and takes approximately 3 hours to complete. Each three-year period, you must complete at minimum 30 PDUs related to agile topics in order to renew your credential. In addition, you must have had at least 12 month of experience with general projects in the last five year. You can also use your PMP(r), PgMP, or other certifications to fulfill this requirement. The certification does not require you to have a degree or certificate in project management.
FAQ
What is the difference between Six Sigma Six Sigma and TQM?
The main difference between these two quality management tools is that six sigma focuses on eliminating defects while total quality management (TQM) focuses on improving processes and reducing costs.
Six Sigma is a method for continuous improvement. It emphasizes the elimination and improvement of defects using statistical methods, such as control charts, P-charts and Pareto analysis.
The goal of this method is to reduce variation in product output. This is achieved by identifying and addressing the root causes of problems.
Total quality management is the measurement and monitoring of all aspects within an organization. This includes training employees to improve their performance.
It is commonly used as a strategy for increasing productivity.
What are the five management process?
The five stages of any business are planning, execution, monitoring, review, and evaluation.
Planning is about setting goals for your future. It includes defining what you want to achieve and how you plan to do it.
Execution occurs when you actually carry out the plans. Everyone involved must follow them.
Monitoring is the process of evaluating your progress toward achieving your objectives. Regular reviews should be done of your performance against targets or budgets.
Reviews take place at the end of each year. They give you an opportunity to review the year and assess how it went. If not, it is possible to make improvements for next year.
Evaluation takes place after the annual review. It helps identify which aspects worked well and which didn't. It also provides feedback regarding how people performed.
What is Kaizen?
Kaizen is a Japanese term which means "continuous improvement." This philosophy encourages employees to continually look for ways to improve the work environment.
Kaizen is built on the belief that everyone should be able do their jobs well.
What are management theories?
Management Concepts are the principles and practices managers use to manage people and resources. These topics include job descriptions, performance evaluations and training programs. They also cover human resource policies, job description, job descriptions, job descriptions, employee motivation, compensation systems, organizational structures, and many other topics.
What is TQM?
When manufacturing companies realized that price was not enough to compete, the industrial revolution brought about the quality movement. If they wanted to stay competitive, they needed to improve their quality and efficiency.
To address this need for improvement management created Total Quality Management (TQM) which aimed to improve all aspects of an organization's performance. It included continuous improvement processes, employee involvement, and customer satisfaction.
Statistics
- The BLS says that financial services jobs like banking are expected to grow 4% by 2030, about as fast as the national average. (wgu.edu)
- Our program is 100% engineered for your success. (online.uc.edu)
- The profession is expected to grow 7% by 2028, a bit faster than the national average. (wgu.edu)
- UpCounsel accepts only the top 5 percent of lawyers on its site. (upcounsel.com)
- Your choice in Step 5 may very likely be the same or similar to the alternative you placed at the top of your list at the end of Step 4. (umassd.edu)
External Links
How To
How can you implement the Kaizen technique?
Kaizen means continuous improvement. Kaizen is a Japanese concept that encourages constant improvement by small incremental changes. This is a collaborative process in which people work together to improve their processes continually.
Kaizen is one of Lean Manufacturing's most efficient methods. Employees responsible for the production line should identify potential problems in the manufacturing process and work together to resolve them. This improves the quality of products, while reducing the cost.
Kaizen is an approach to making every worker aware and alert to what is happening around them. So that there is no problem, you should immediately correct it if something goes wrong. It is important that employees report any problems they see while on the job to their managers.
Kaizen follows a set of principles. We always start from the end product and move toward the beginning. If we want to improve our factory for example, we start by fixing the machines that make the final product. Then, we fix the machines that produce components and then the ones that produce raw materials. Then we fix the workers, who directly work with these machines.
This method is known as kaizen because it focuses upon improving every aspect of the process step by step. We finish fixing the factory and then go back to the beginning. This continues until we achieve perfection.
To implement kaizen in your business, you need to find out how to measure its effectiveness. There are many ways you can determine if kaizen has been implemented well. Another way to determine if kaizen is working well is to look at the quality of the products. Another way is to see how much productivity has increased since implementing kaizen.
If you want to find out if your kaizen is actually working, ask yourself why. Is it because the law required it or because you want to save money. It was a way to save money or help you succeed.
Let's say you answered yes or all of these questions. Congratulations! You're ready to start kaizen.