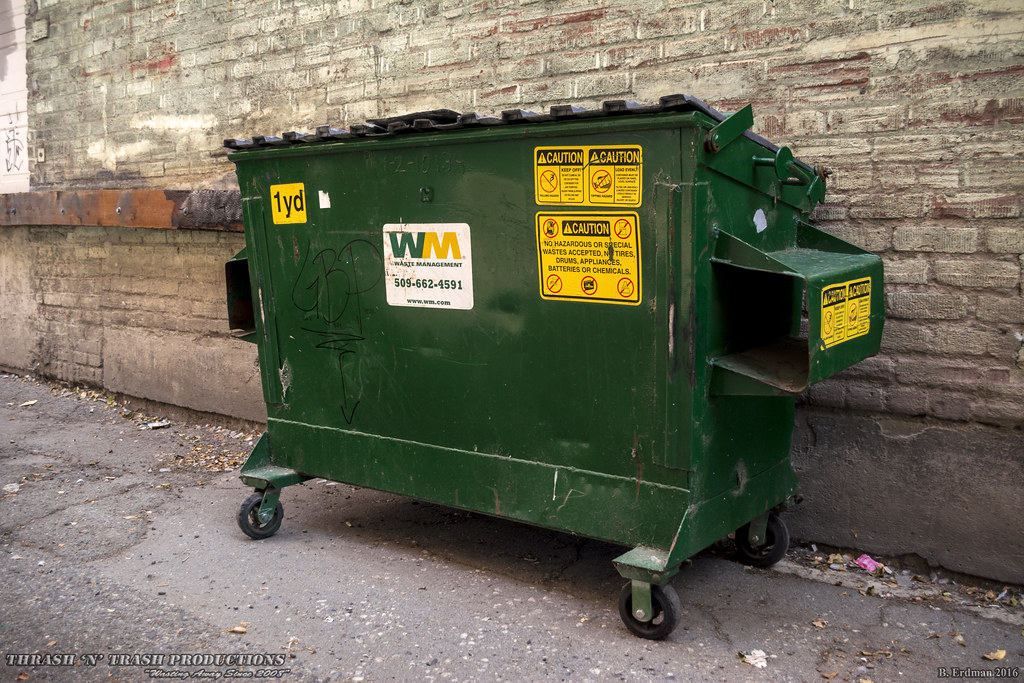
There are four fundamental management perspectives. These perspectives are Theory and Function, Historical Development, Future Trends, and Function. This article discusses these perspectives. Each perspective comes with its own advantages and disadvantages. It is important to understand the difference between each perspective. This will allow you to pick the one that best suits you and your preferences. Here are some examples.
Theories of Management
Theories of management are important in determining the appropriate management strategy for an organization. Different theories of management focus on different aspects. However, they all relate to management. A combination of different theories may produce more effective results. Modern organizations are more flexible because they use a variety of theories.
Different contexts can use theories about management. These include project management as well as general management. In the project management context, they can be viewed as condensed pieces of knowledge that enable novices to do what an expert would do. These techniques are most effective when they are applied in a small project environment, where theoretical issues can be addressed without imposing additional penalties. However, they can lead to serious performance problems and other issues in large projects that could have avoided with better management.
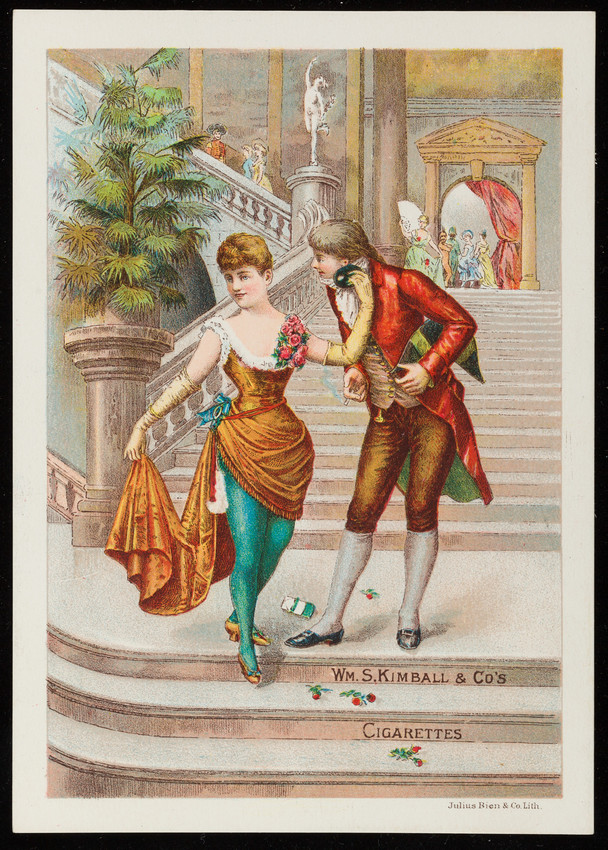
Management functions
For an organisation to succeed, its management functions are essential. They are responsible for determining the needs of an organisation, monitoring its performance, and implementing corrective measures if necessary. The management role plays a major part in any organization, particularly when it comes reaching goals for profit and market share. Managers must make decisions, set goals, implement strategies and track the progress of various parts of an organization.
Planning is the first step in the managerial process. It involves defining and assessing the goals. This requires an ability to analyze and understand past and current trends as well as the ability develop and implement future strategies. These functions can be performed well and an organisation will achieve its goals without any difficulties.
Historical development
Management has changed over the years, with new theories placing more emphasis on human factors. Douglas McGregor's Theory Y, which is a well-known example of this change, is a great example. It also transformed the traditional idea of what executives do. Instead of being the masters of their organizations, they became coaches. Organizational theorists began to explore the concept of emotional intelligence and the human element in management, and the emphasis on this factor was fundamentally changed.
Management theory was a hot topic after the Industrial Revolution. This was a significant turning point in management's history. The changes that followed led to the development of six management theories. Each theory addresses different aspects management.
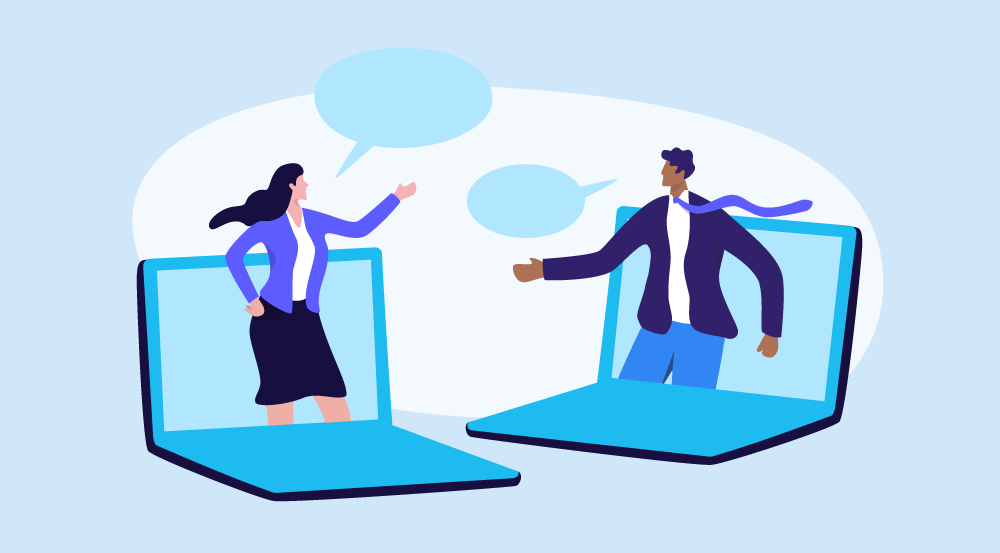
Future trends
A series of trends are shaping the future of management. One of these trends concerns the changing role that managers play. Managers must be flexible and agile in order to fulfill this role. Flexibility in work is becoming more standard for managers in the UK. Flexible working is becoming more common in the UK. More than half of managers anticipate flexible work within five years. Half of direct reports believe they are being more flexible than five year ago.
A trend that is affecting management is the importance of working relationships. Managers are now more aware of this trend than ever and feel that working relationships are even more important today than they were five or six years ago. The emergence of flexible working environments is contributing to this trend. People have been forced to put more importance on trust and personal relationships due to the recent economic crisis. These trends can be used to help companies recruit, develop, retain and motivate employees.
FAQ
How does a manager motivate their employees?
Motivation refers to the desire to perform well.
You can get motivated by doing something enjoyable.
You can also be motivated by the idea of making a difference to the success and growth of your organization.
For example, if you want to become a doctor, you'll probably find it more motivating to see patients than to study medicine books all day.
Another source of motivation is within.
You might feel a strong sense for responsibility and want to help others.
Or you might enjoy working hard.
If you don't feel motivated, ask yourself why.
Next, think of ways you can improve your motivation.
How do you manage your employees effectively?
Achieving employee happiness and productivity is key to managing them effectively.
It is important to set clear expectations about their behavior and keep track of their performance.
Managers need clear goals to be able to accomplish this.
They need to communicate clearly with staff members. And they need to ensure that they reward good performance and discipline poor performers.
They will also need to keep records about their team's activities. These include:
-
What did you accomplish?
-
How much work did you put in?
-
Who did it all?
-
Was it done?
-
Why it was done?
This information is useful for monitoring performance and evaluating the results.
How does Six Sigma work
Six Sigma uses statistical analysis to find problems, measure them, analyze root causes, correct problems, and learn from experience.
The first step is identifying the problem.
The data is then analyzed and collected to identify trends.
Then corrective actions are taken to solve the problem.
Finally, the data are reanalyzed in order to determine if it has been resolved.
This continues until you solve the problem.
What kind of people use Six Sigma?
People who have worked with statistics and operations research will usually be familiar with the concepts behind six sigma. However, anyone involved in any aspect of business can benefit from using it.
This requires a lot of dedication, so only people with great leadership skills can make the effort to implement it.
Statistics
- This field is expected to grow about 7% by 2028, a bit faster than the national average for job growth. (wgu.edu)
- The average salary for financial advisors in 2021 is around $60,000 per year, with the top 10% of the profession making more than $111,000 per year. (wgu.edu)
- Your choice in Step 5 may very likely be the same or similar to the alternative you placed at the top of your list at the end of Step 4. (umassd.edu)
- The BLS says that financial services jobs like banking are expected to grow 4% by 2030, about as fast as the national average. (wgu.edu)
- UpCounsel accepts only the top 5 percent of lawyers on its site. (upcounsel.com)
External Links
How To
How does Lean Manufacturing work?
Lean Manufacturing is a method to reduce waste and increase efficiency using structured methods. These processes were created by Toyota Motor Corporation, Japan in the 1980s. It was designed to produce high-quality products at lower prices while maintaining their quality. Lean manufacturing emphasizes removing unnecessary steps from the production process. It is made up of five elements: continuous improvement, continuous improvement, just in-time, continuous change, and 5S. Pull systems are able to produce exactly what the customer requires without extra work. Continuous improvement is the continuous improvement of existing processes. Just-in–time refers when components or materials are delivered immediately to their intended destination. Kaizen refers to continuous improvement. It is achieved through small changes that are made continuously. The 5S acronym stands for sort in order, shine standardize and maintain. These five elements can be combined to achieve the best possible results.
Lean Production System
Six key concepts make up the lean manufacturing system.
-
Flow - focuses on moving information and materials as close to customers as possible.
-
Value stream mapping is the ability to divide a process into smaller tasks, and then create a flowchart that shows the entire process.
-
Five S’s - Sorted, In Order. Shine. Standardize. And Sustain.
-
Kanban: Use visual signals such stickers, colored tape, or any other visual cues, to keep track your inventory.
-
Theory of constraints: Identify bottlenecks and use lean tools such as kanban boards to eliminate them.
-
Just-in-time - deliver components and materials directly to the point of use;
-
Continuous improvement: Make incremental improvements to the process instead of overhauling it completely.