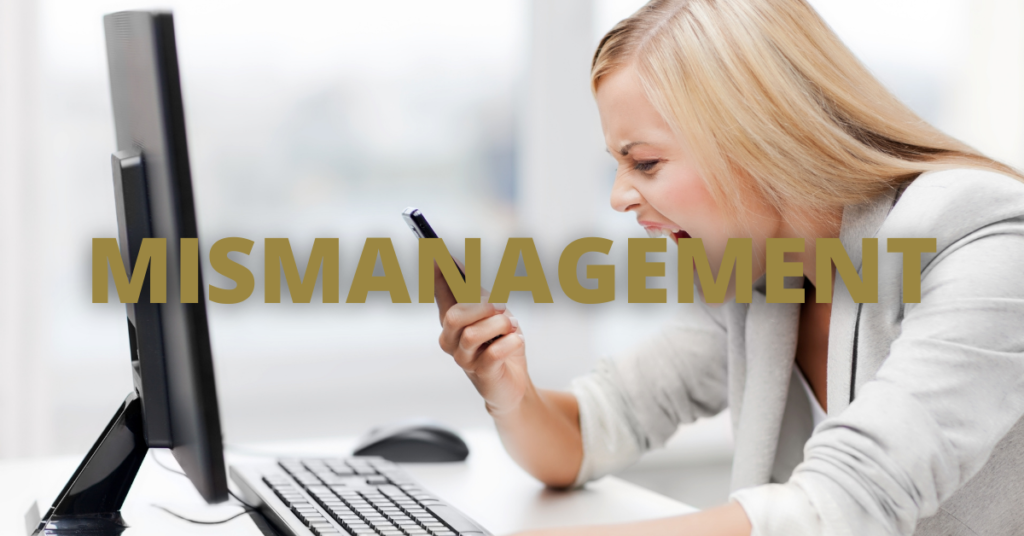
You should think about several things when thinking about a career in supply-chain management. There are many supply chain types, and different industries have various supply chains. A supply chain manager working for a manufacturing company is not the best fit for someone who wants to work for a wholesale company or retail business.
Characteristics of a successful supply chain manager
Supply chain managers who excel are adaptable learners who are open to learning and willing to experiment with new ideas. They are quick to understand the nuances of a problem and use failures as clues to improve. They enjoy the challenge of new tasks and can quickly grasp the essence of any topic. Their curiosity and insatiable hunger for knowledge fuels their passion to learn more.
Although supply chain managers should not become micromanagers, they must be able to take strategic risks. Growth is not without risks, but data must back them up. This requires being strategic and analytical, not reactive. Inflexibility impedes success. It also makes a supply chain manager frustrated with the process.
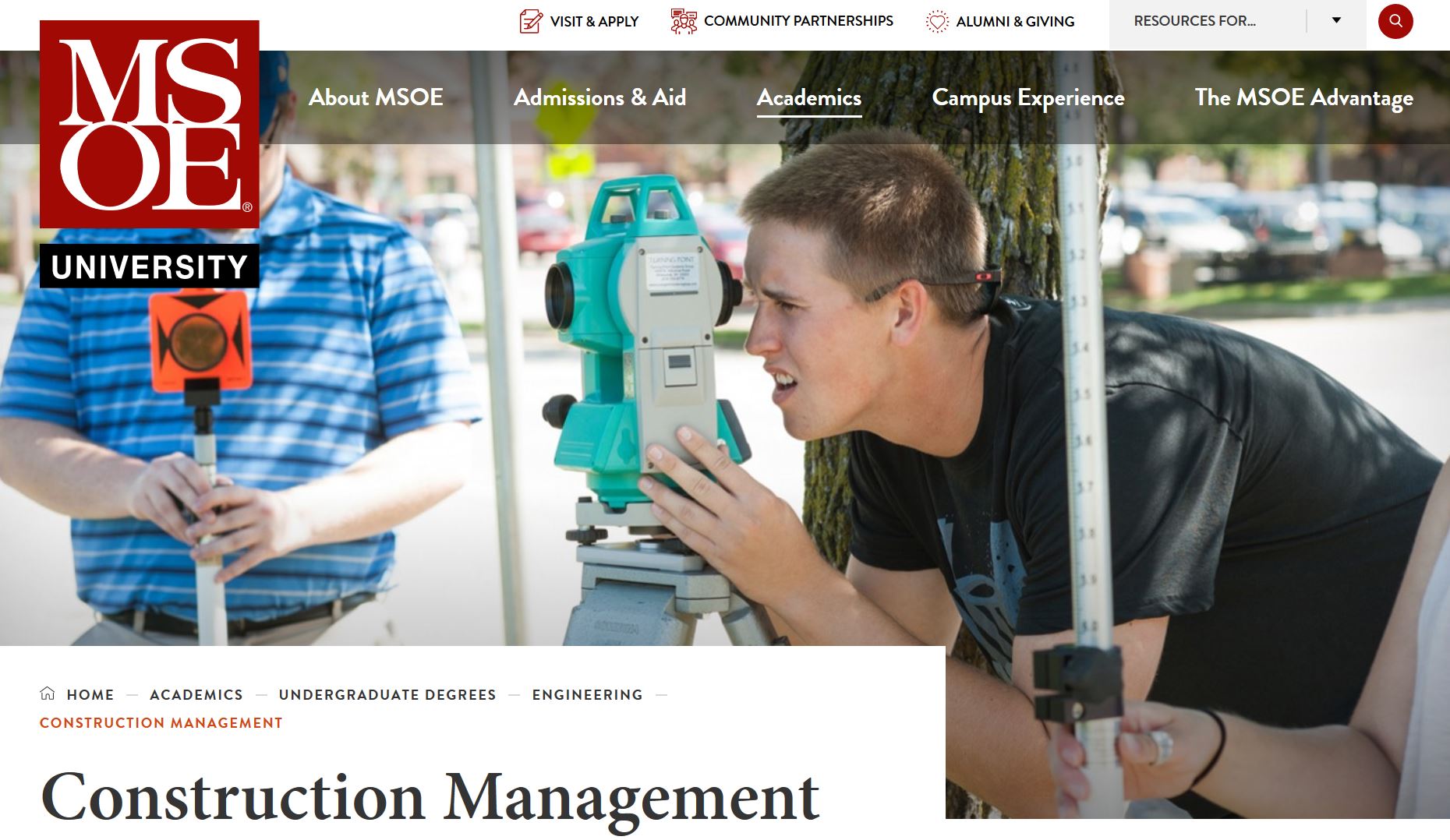
Managing a supply chain is a complex and ever-changing field. Supply chain managers must keep up to date with market trends, and also be proactive in the implementation of new technology. They must also be able communicate effectively with those with advanced technological knowledge.
The requirements for a bachelor's in supply chain management
A bachelor's degree for supply chain management provides students with a foundation in leadership, strategic management and business administration. This degree also teaches common software skills. A degree in supply-chain management that is accredited can be obtained for a relatively affordable price. In 2020, full-time programs at public four-year universities cost in-state students on average $10,560 per annum, compared with $37.650 at private universities. Financial aid is available to help reduce the amount. Federal student loans are also available to finance your degree.
An accredited university may offer an online degree in supply-chain management. This can be a great option. The program covers international supply chains and global supply chains as well as business decision-making. Other coursework in the program covers operational strategies and sustainability in global supply chains. The program costs about $688 an hour.
Typical job duties of a supply chain manager
Managers of the supply chain are responsible to organize a company’s supply network. They plan and manage the flow of products and inventory and develop and implement processes to reduce costs. They manage third-party logistics providers and identify waste. They create monthly, weekly, or daily reports based on their performance metrics.

Most supply chain managers work forty hours per semaine and are often located in business settings, sometimes far from the manufacturing floor. The role requires a deep understanding of the business and operations as well as all aspects of the organization. They typically must be comfortable working with people and data. A career as a supply-chain manager is a great choice if you like following processes and working with ideas.
A supply chain manager earns slightly more than a director in procurement. These two roles require similar skills in logistics, customer service, and procedures.
FAQ
What does the term "project management” mean?
Management is the act of managing activities in order to complete a project.
This includes defining the scope, identifying the requirements and preparing the budget. We also organize the project team, schedule the work, monitor progress, evaluate results, and close the project.
How do you effectively manage employees?
Effectively managing employees means making sure they are productive and happy.
It means setting clear expectations for them and keeping an eye on their performance.
Managers need clear goals to be able to accomplish this.
They should communicate clearly to staff members. They also need to make sure that they discipline and reward the best performers.
They must also keep records of team activities. These include:
-
What was the result?
-
What was the work involved?
-
Who did it?
-
Was it done?
-
Why was this done?
This information is useful for monitoring performance and evaluating the results.
What kind people use Six Sigma?
Six-sigma will be well-known to anyone who has worked in operations research or statistics. But anyone can benefit from it.
This requires a lot of dedication, so only people with great leadership skills can make the effort to implement it.
What's the difference between a program and a project?
A project is temporary; a program is permanent.
A project is usually defined by a clear goal and a set deadline.
It is often done in a team that reports to another.
A program often has a set goals and objectives.
It is typically done by one person.
What are management concepts?
Management Concepts are the principles and practices managers use to manage people and resources. These include topics such as human resource policies and job descriptions, performance assessments, training programs and employee motivation.
What are the main four functions of management
Management is responsible to plan, organize, direct, and control people and resources. This includes setting goals, developing policies and procedures, and creating procedures.
Management is the ability to direct, coordinate, control, motivate, supervise, train, and evaluate an organization's efforts towards achieving its goals.
The following are the four core functions of management
Planning - Planning refers to deciding what is needed.
Organizing is the act of deciding how things should go.
Directing - This refers to getting people follow instructions.
Controlling: Controlling refers to making sure that people do what they are supposed to.
How can we create a successful company culture?
A positive company culture creates a sense of belonging and respect in its people.
It is based on three principles:
-
Everyone has something valuable to contribute
-
People are treated fairly
-
Respect is shared between individuals and groups
These values reflect in how people behave. They will treat others with kindness and consideration.
They will respect the opinions of others.
They encourage others to express their feelings and ideas.
In addition, the company culture encourages open communication and collaboration.
People feel free to express their views openly without fear of reprisal.
They understand that errors will be tolerated as long they are corrected honestly.
Finally, the company culture encourages honesty as well as integrity.
Everyone understands that the truth is always best.
Everyone understands that there are rules and regulations which apply to them.
People don't expect special treatment or favors.
Statistics
- The BLS says that financial services jobs like banking are expected to grow 4% by 2030, about as fast as the national average. (wgu.edu)
- Your choice in Step 5 may very likely be the same or similar to the alternative you placed at the top of your list at the end of Step 4. (umassd.edu)
- The profession is expected to grow 7% by 2028, a bit faster than the national average. (wgu.edu)
- UpCounsel accepts only the top 5 percent of lawyers on its site. (upcounsel.com)
- The average salary for financial advisors in 2021 is around $60,000 per year, with the top 10% of the profession making more than $111,000 per year. (wgu.edu)
External Links
How To
How is Lean Manufacturing done?
Lean Manufacturing is a method to reduce waste and increase efficiency using structured methods. They were developed in Japan by Toyota Motor Corporation (in the 1980s). The primary goal was to make products with lower costs and maintain high quality. Lean manufacturing eliminates unnecessary steps and activities from a production process. It includes five main elements: pull systems (continuous improvement), continuous improvement (just-in-time), kaizen (5S), and continuous change (continuous changes). The production of only what the customer needs without extra work is called pull systems. Continuous improvement refers to continuously improving existing processes. Just-in-time refers to when components and materials are delivered directly to the point where they are needed. Kaizen means continuous improvement. Kaizen involves making small changes and improving continuously. Fifth, the 5S stand for sort, set up in order to shine, standardize, maintain, and standardize. These five elements work together to produce the best results.
The Lean Production System
The lean production system is based on six key concepts:
-
Flow - focus on moving material and information as close to customers as possible;
-
Value stream mapping - break down each stage of a process into discrete tasks and create a flowchart of the entire process;
-
Five S's, Sort, Set in Order, Shine. Standardize. and Sustain.
-
Kanban - use visual signals such as colored tape, stickers, or other visual cues to keep track of inventory;
-
Theory of Constraints - Identify bottlenecks in the process, and eliminate them using lean tools such kanban boards.
-
Just-in-time delivery - Deliver components and materials right to your point of use.
-
Continuous improvement - make incremental improvements to the process rather than overhauling it all at once.