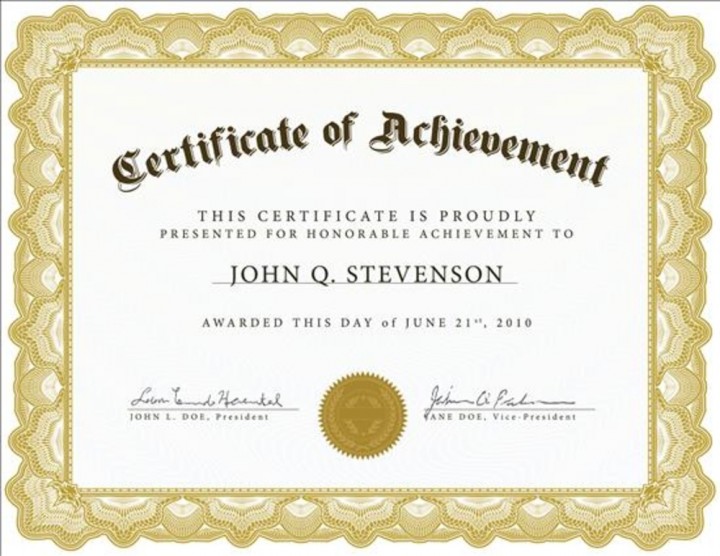
Online learning is becoming the preferred mode of education for many people, and it offers many benefits to students. Online learning can improve retention rates, encourage self-direction, increase flexibility, and promote self-direction. But, there are also some downsides. Online learning has the potential to disrupt a student's emotional state. Students can experience negative emotions and have difficulty concentrating on information.
Self-direction
Online learning has many benefits for self-directed learners. This method of learning is more flexible and can be used to teach multiple subjects. Lessons can help students learn skills that will be useful in the 21st century. Real-world projects include meal planning and maintaining a healthy lifestyle, as well as traveling, child care, and applying to jobs. Self-directed learning experiences help students develop decision-making skills, as well as communication and resourcefulness skills.

Online learning does not have all the positives. It is not suitable for people who are new to self-directed learning. Without a mentor or instructor, the learning process is more difficult and less effective. Students are less likely to collaborate on content, share ideas, or discuss difficult topics together. However, as more organisations are realising, the benefits of self-directed learning are substantial and impressive.
Flexibility
Online learning provides students with more choice and flexibility. This benefit has been acknowledged by its proponents. This flexibility reduces geographic, time, and speed barriers. Online learning has its downsides. To get the most from online learning, students need to be able to manage their time. In addition, gender may impact a student's temporal flexibility. A recent study of 380,000 students found that gender and learner time management behaviors predicted the likelihood of completing a course. Although there was no conclusive evidence, these results indicate what is generally believed.
Flexibility is crucial for modern student's lives. Many students find it hard to make class attendance due to the demands of school life or work. Flexible learning allows students to schedule their studies around work and school, making it easier to manage their time. Students can also speed up their degree at a pace that suits them, which can increase retention.
Increased retention
Engaging instructors and online courses are essential to encourage high levels of interaction and dialogue. This is especially true for online classes that don't use video conferencing. Although it is impossible for online students to replicate the experience of being in person, it is important that they feel connected to the campus community. Engaging lessons can help students learn and connect to the campus culture. This increases student retention in all types of institutions.
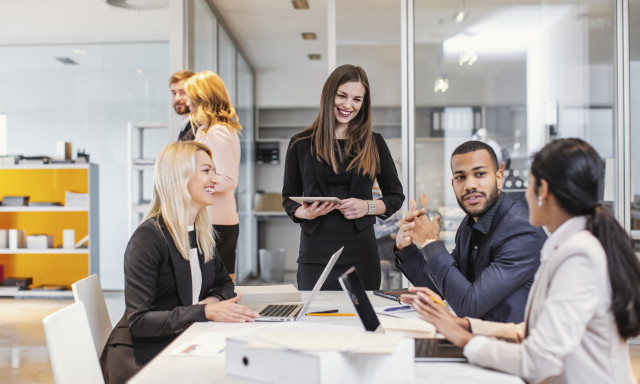
Low retention can be due to many factors. Students with different norm values may have difficulty interacting with their peers and feel alienated in an institution's social network. They may drop out of classes as a result. The constructivist nature and difficulty of motivating students can also be a problem with online courses. Instructors assume that students can be digital natives. This is often false.
FAQ
What is the difference between project and program?
A project is temporary; a program is permanent.
A project typically has a defined goal and deadline.
It is often performed by a team of people, who report back on someone else.
A program often has a set goals and objectives.
It is usually implemented by a single person.
What is TQM?
The quality movement was born during the industrial revolution when manufacturing companies realized they could not compete on price alone. If they wanted to stay competitive, they needed to improve their quality and efficiency.
Management realized the need to improve and created Total Quality Management, which focused on improving all aspects within an organization's performance. It included continual improvement processes, employee involvement, customer satisfaction, and customer satisfaction.
Why is project management important for companies?
Project management techniques ensure that projects run smoothly while meeting deadlines.
This is because most businesses rely heavily on project work to produce goods and services.
Companies must manage these projects effectively and efficiently.
Companies could lose their time, reputation, and money without effective project management.
What's the difference between Six Sigma and TQM?
The key difference between the two quality management tools is that while six-sigma focuses its efforts on eliminating defects, total quality management (TQM), focuses more on improving processes and reducing cost.
Six Sigma is a method for continuous improvement. This approach emphasizes eliminating defects through statistical methods like control charts, Pareto analysis, and p-charts.
This method seeks to decrease variation in product output. This is done by identifying and correcting the root causes of problems.
Total quality management involves measuring and monitoring all aspects of the organization. Training employees is also part of total quality management.
It is frequently used as an approach to increasing productivity.
How can we make our company culture successful?
A positive company culture creates a sense of belonging and respect in its people.
It's founded on three principal principles:
-
Everybody has something of value to share
-
People are treated fairly
-
There is mutual respect between individuals and groups
These values can be seen in the behavior of people. They will show consideration and courtesy to others.
They will respect the opinions of others.
These people will inspire others to share thoughts and feelings.
Company culture also encourages open communication, collaboration, and cooperation.
People feel safe to voice their opinions without fear of reprisal.
They are aware that mistakes can be accepted if they are treated honestly.
Finally, the company culture promotes honesty and integrity.
Everyone knows that they must always tell the truth.
Everyone understands that there are rules and regulations which apply to them.
Nobody expects to be treated differently or given favors.
Statistics
- The profession is expected to grow 7% by 2028, a bit faster than the national average. (wgu.edu)
- As of 2020, personal bankers or tellers make an average of $32,620 per year, according to the BLS. (wgu.edu)
- 100% of the courses are offered online, and no campus visits are required — a big time-saver for you. (online.uc.edu)
- Your choice in Step 5 may very likely be the same or similar to the alternative you placed at the top of your list at the end of Step 4. (umassd.edu)
- This field is expected to grow about 7% by 2028, a bit faster than the national average for job growth. (wgu.edu)
External Links
How To
How can you implement the Kaizen technique?
Kaizen means continuous improvement. The Japanese philosophy emphasizes small, incremental improvements to achieve continuous improvement. This term was created by Toyota Motor Corporation in 1950. It's a process where people work together to improve their processes continuously.
Kaizen, a Lean Manufacturing method, is one of its most powerful. The concept involves employees responsible for manufacturing identifying problems and trying to fix them before they become serious issues. This improves the quality of products, while reducing the cost.
Kaizen is about making everyone aware of the world around them. If something is wrong, it should be corrected immediately so that no problem occurs. So, if someone notices a problem while working, he/she should report it to his/her manager.
When doing kaizen, there are some principles we must follow. We always start from the end product and move toward the beginning. If we want to improve our factory for example, we start by fixing the machines that make the final product. First, we fix machines that produce components. Next, we fix machines that produce raw material. Then we fix the workers, who directly work with these machines.
This is known as "kaizen", because it emphasizes improving each step. Once we have finished fixing the factory, we return to the beginning and work until perfection.
To implement kaizen in your business, you need to find out how to measure its effectiveness. There are many methods to assess if kaizen works well. One method is to inspect the finished products for defects. Another way is to check how much productivity has grown since kaizen was implemented.
Another way to know whether kaizen is working is to ask yourself why did you decide to implement kaizen. You were trying to save money or obey the law? It was a way to save money or help you succeed.
If you answered yes to any one of these questions, congratulations! Now you're ready for kaizen.