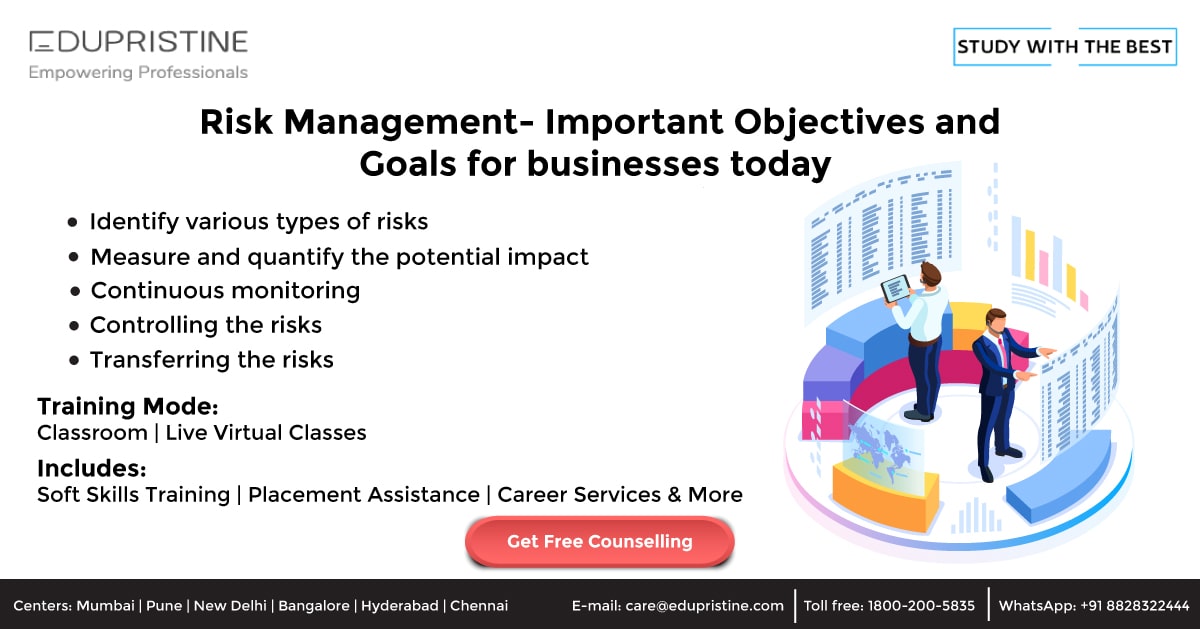
Proper waste disposal must be considered when managing chemicals wastes from manufacturing plants. To avoid toxic fumes from forming, incompatible chemicals should be stored at different secondary containment locations. Incompatible chemicals should never be mixed together with other chemicals.
Hazards
To avoid potential health and environmental problems, it is essential to properly dispose off chemical waste. Proper disposal requires identifying which chemical waste streams should be disposed. This usually happens at the end of an experiment. In some cases, hazardous wastes may be mixed with normal waste in order to save money. However, this is not an option.
You must ensure that the MSDSs of hazardous chemicals are checked before you store them. These MSDSs are often online or available from the manufacturer. These contain information regarding the hazards of chemical substances, such as their quantity and composition. Additionally, they include recommended emergency procedures, such how to handle spills.
Regulations
Chemical waste management rules govern chemical waste disposal in all workplaces, from manufacturing plants to laboratories. However, most chemical wastes can be generated in laboratories. There are also other types which are not directly related to labs. These include contaminated soils, building materials, paints and lubricants. Expired chemicals can also be disposed off according to rules.
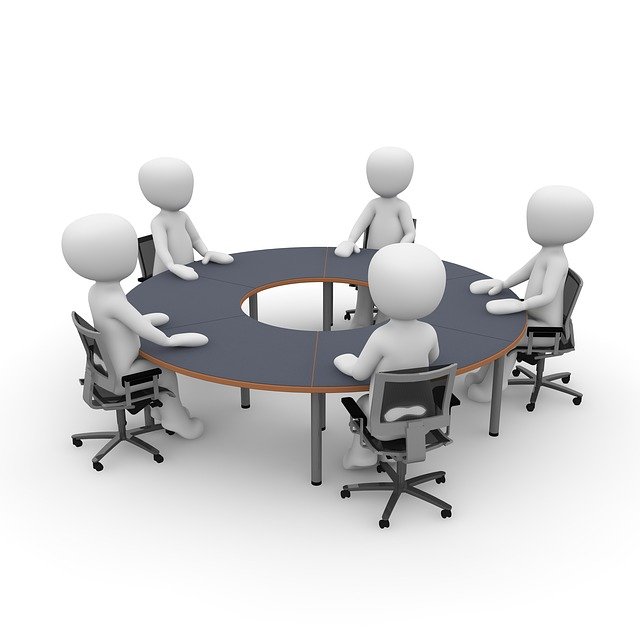
Proper handling of hazardous substances is an integral part safety protocols. It is the responsibility and obligation of employees. This is done in order to reduce personal exposure and the risk of environmental contamination. Two University programs are available to assist employees with complying with regulations.
Collection
The first step in the collection process is to fill out the Chemical Collection Request Form. This form must also be completed for each waste container. Often, multiple containers of the same chemical waste are combined into a single request. This form is then sent online. After submitting your request online, you'll receive a CCR Number and Dangerous Waste Label for your waste container. Once you have received the information, you will be able to print the label and attach it onto your waste container label.
Chemical waste can be any substance or mixture of chemicals that is no longer used. These materials can be either in solid, liquid, and gaseous forms. To avoid pollution charges, it is crucial to collect chemical waste.
Storage
It is important to maintain proper chemical waste storage practices to avoid contamination. Separate wastes according the hazard type to avoid contamination. All wastes should be kept in compatible containers. For example, chemical wastes containing hydrofluoric acid should not be stored in glass or metal containers. For liquids-containing wastes, containers should be designed for liquids. If the containers are too small to hold large quantities, they should transfer to larger containers.
Containers should be tightly sealed. Containers should be sealed tightly to prevent leakage. Containers that contain contaminated glassware should be puncture-proof. Also, the containers should be marked hazardous waste.
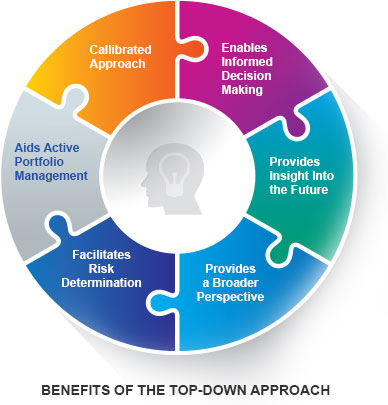
Disposal
If your company produces hazardous waste, it is important to know the proper disposal procedure. Hazardous wastes are regulated by the Texas Commission on Environmental Quality and the Environmental Protection Agency, and improper disposal may result in substantial fines and legal action. This type of waste should be managed through a hazardous material management system.
Chemical waste is the waste of chemicals that have no further use. These chemicals come in many different forms. Some are considered dangerous, while others can be used for their own good. Some chemical wastes can be universally hazardous while others may be household hazardous. For a chemical to be considered hazardous, it must demonstrate four characteristics. They can be toxic, radioactive, flammable, or biohazardous. Some chemicals may need to be kept safe in special containers.
FAQ
What are the five management processes?
The five stages of a business include planning, execution (monitoring), review, evaluation, and review.
Setting goals for the future requires planning. It involves setting goals and making plans.
Execution occurs when you actually carry out the plans. These plans must be adhered to by everyone.
Monitoring allows you to monitor your progress towards achieving your goals. Regular reviews of performance against targets, budgets, and other goals should be part.
Each year, reviews are held at the end. They are a chance to see if everything went smoothly during the year. If not, changes may be made to improve the performance next time around.
Evaluation takes place after the annual review. It helps you identify the successes and failures. It also provides feedback on how well people performed.
How does a manager motivate his/her employees?
Motivation is the desire for success.
Enjoyable activities can motivate you.
Another way to get motivated is to see yourself as a contributor to the success of the company.
If you are a doctor and want to be one, it will likely be more rewarding to see patients than to read medical books every day.
A different type of motivation comes directly from the inside.
Perhaps you have a strong sense to give back, for example.
Perhaps you enjoy working hard.
Ask yourself why you aren't feeling motivated.
You can then think of ways to improve your motivation.
What are the main four functions of management
Management is responsible for organizing, managing, directing and controlling people, resources, and other activities. This includes setting goals, developing policies and procedures, and creating procedures.
Management aids an organization in reaching its goals by providing direction and coordination, control, leadership motivation, supervision, training, evaluation, and leadership.
The four main functions of management are:
Planning – Planning involves deciding what needs to happen.
Organizing – Organizing means deciding how to organize things.
Direction - This is the art of getting people to follow your instructions.
Controlling – This refers to ensuring that tasks are carried out according to plan.
What are the key management skills?
Business owners need to have management skills, no matter how small or large they may be. They are the ability to manage people and finances, space, money, and other factors.
These skills are necessary for setting goals and objectives as well as planning strategies, leading groups, motivating employees and solving problems.
As you can see, there's no end to the list of managerial duties!
What is a basic management tool that can be used for decision-making?
A decision matrix is an easy but powerful tool to aid managers in making informed decisions. It helps them to think strategically about all options.
A decision matrix represents alternatives in rows and columns. This makes it easy for you to see how each option affects other options.
In this example, we have four possible alternatives represented by the boxes on the left side of the matrix. Each box represents an option. The top row shows the status quo (the current situation), and the bottom row shows what would happen if nothing was done at all.
The effect of choosing Option 1 can be seen in column middle. In this case, it would mean increasing sales from $2 million to $3 million.
The effects of options 2 and 3 are shown in the next columns. These positive changes can increase sales by $1 million or $500,000. They also have negative consequences. For instance, Option 2 increases cost by $100 thousand while Option 3 reduces profits by $200 thousand.
The last column displays the results of selecting Option 4. This would result in a reduction of sales of $1 million.
The best part of using a decision-matrix is that it doesn't require you to know which numbers belong where. The best thing about a decision matrix is that you can simply look at the cells, and immediately know whether one option is better or not.
This is because the matrix has done all the hard work. Simply compare the numbers within the cells.
Here's an example of how you might use a decision matrix in your business.
Advertising is a decision that you make. This will allow you to increase your revenue by $5000 per month. You will still have to pay $10000 per month in additional expenses.
By looking at the cell just below "Advertising", the net result can be calculated as $15 thousand. Advertising is a worthwhile investment because it has a higher return than the costs.
How does Six Sigma work?
Six Sigma uses statistics to measure problems, find root causes, fix them, and learn from past mistakes.
The first step in solving a problem is to identify it.
Next, data is collected and analyzed to identify trends and patterns.
Next, corrective steps are taken to fix the problem.
The data are then reanalyzed to see if the problem is solved.
This cycle will continue until the problem is solved.
Statistics
- The average salary for financial advisors in 2021 is around $60,000 per year, with the top 10% of the profession making more than $111,000 per year. (wgu.edu)
- UpCounsel accepts only the top 5 percent of lawyers on its site. (upcounsel.com)
- As of 2020, personal bankers or tellers make an average of $32,620 per year, according to the BLS. (wgu.edu)
- Hire the top business lawyers and save up to 60% on legal fees (upcounsel.com)
- This field is expected to grow about 7% by 2028, a bit faster than the national average for job growth. (wgu.edu)
External Links
How To
How do you apply the Kaizen method to your life?
Kaizen means continuous improvement. Kaizen is a Japanese concept that encourages constant improvement by small incremental changes. It is a process where people come together to improve their processes.
Kaizen is one of the most effective methods used in Lean Manufacturing. This concept requires employees to identify and solve problems during manufacturing before they become major issues. This is how you can improve the quality and lower the cost.
Kaizen is an approach to making every worker aware and alert to what is happening around them. Correct any errors immediately to avoid future problems. It is important that employees report any problems they see while on the job to their managers.
Kaizen is based on a few principles. Start with the end product, and then move to the beginning. For example, if we want to improve our factory, we first fix the machines that produce the final product. First, we fix machines that produce components. Next, we fix machines that produce raw material. Then we fix the workers, who directly work with these machines.
This is known as "kaizen", because it emphasizes improving each step. After we're done with the factory, it's time to go back and fix the problem.
You need to know how to measure the effectiveness of kaizen within your business. There are many ways you can determine if kaizen has been implemented well. Another way to determine if kaizen is working well is to look at the quality of the products. Another way is determining how much productivity increased after implementing kaizen.
Another way to know whether kaizen is working is to ask yourself why did you decide to implement kaizen. Is it because the law required it or because you want to save money. Did you really believe that it would be a success factor?
Let's say you answered yes or all of these questions. Congratulations! Now you're ready for kaizen.