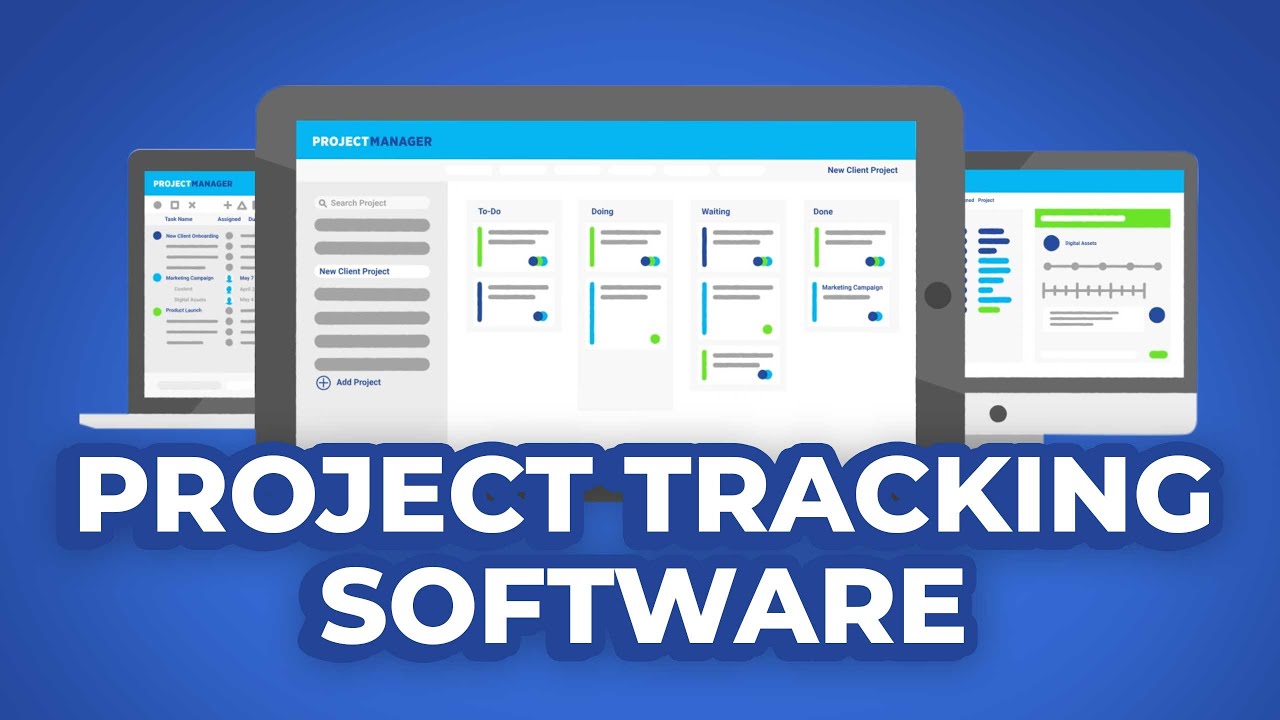
The hierarchy of controls is an effective way for workers to be protected from potential hazards. It is used in many industries, and it is widely recognized by many safety organisations. This concept is adopted by industry managers and promoted as a standard practice. There are many variations to this system. Learn more by visiting our guide to NFPA70E hazard classified system and ARECC variation. Once you have this information, you can better apply the hierarchy to your workplace.
NFPA70E
NFPA70E consists of a series of standards for workplace safety. The new 2018 edition has a new section called Annex Q that describes human performance and human error and their potential negative consequences. This section also includes a hierarchy, which prioritizes eliminating hazards. In the case of electrical hazards, eliminating the source of energy or hazard is the first step. Only as a last resort, personal protective equipment should not be used.
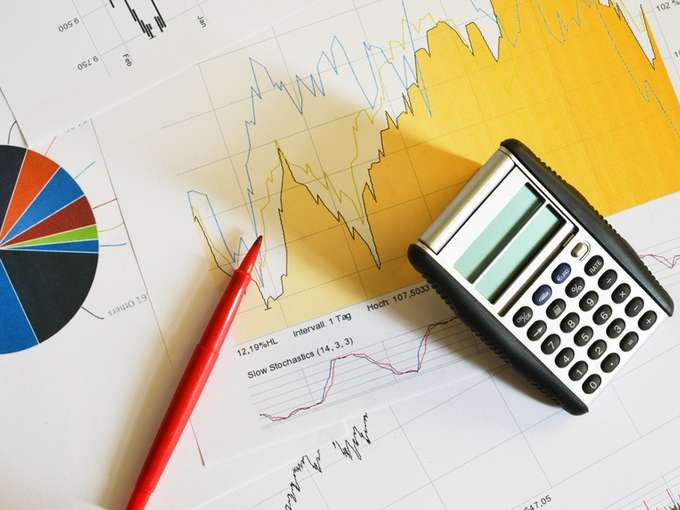
The next step is to determine the level of exposure to hazards and determine the appropriate engineering controls to reduce the severity of the risks. While engineering controls may reduce the danger from hazardous substances, they do not eliminate it completely. The hierarchy of control aims to minimize hazards and to prevent their severity. An example of engineering control is a fog or vapor machine, ventilation system or fire alarm.
The NFPA 70E standard also includes appendices. These are documents that detail specific procedures and practices, and they provide guidance on how to do them. Appendices contain sample forms, PPE guidance and design requirements as well as risk assessment guidelines. As with the main text, the annexes are meant to provide guidance on how to implement the standard. In certain cases, they might provide useful information to help in the safety of a building and/or workplace.
Variation of ARECC
The ARECC Variation in the Hierarchy of Control is a method of reducing the exposure to a given hazard. This system has been used for decades in the United States of America and Canada. It has also been adopted in other countries. For example, some countries use isolation to prevent engineering control, while others combine them both. The ARECC version includes employee training as well as warnings. Important to understand that warnings can't eliminate all hazards from a workplace.
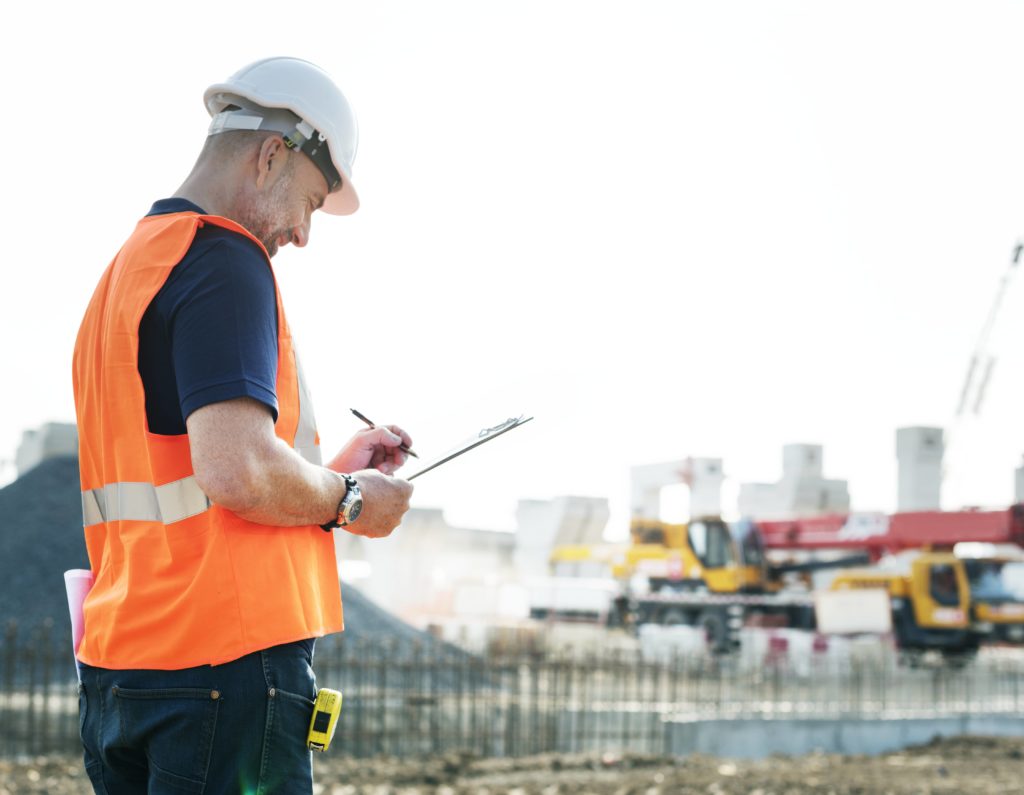
The ARECC hierarchy and controls are a framework for occupational health and safety. It determines possible solutions and prioritizes them according the effectiveness. In the hierarchy, there are five categories: engineering controls; administrative controls; personal protective equipment; and administrative controls. Each category has specific strengths and weaknesses that are important for a particular situation. Some of the controls that are included in the ARECC hierarchy are more effective than others.
FAQ
What are the three main management styles you can use?
These are the three most common management styles: participative (authoritarian), laissez-faire (leavez-faire), and authoritarian. Each style is unique and has its strengths as well as weaknesses. Which style do yo prefer? Why?
Authoritarian – The leader sets a direction and expects everyone follows it. This style works best if the organization is large and stable.
Laissez-faire – The leader gives each individual the freedom to make decisions for themselves. This style is most effective when the organization's size and dynamics are small.
Participative – Leaders are open to suggestions and ideas from everyone. This style works best in smaller organizations where everyone feels valued.
How to manage employees effectively?
Effectively managing employees requires that you ensure their happiness and productivity.
It also means having clear expectations of their behavior and keeping track of their performance.
Managers need clear goals to be able to accomplish this.
They need to communicate clearly with staff members. They must communicate clearly with staff members.
They should also keep records of all activities within their team. These include:
-
What did you accomplish?
-
How much work did you put in?
-
Who did it, anyway?
-
It was done!
-
Why did it happen?
This information can be used for monitoring performance and evaluating results.
Why is it important that companies use project management methods?
Project management techniques ensure that projects run smoothly while meeting deadlines.
This is because most businesses rely on project work for their products and services.
Companies need to manage these projects efficiently and effectively.
Companies could lose their time, reputation, and money without effective project management.
What do we mean when we say "project management"?
It refers to the management of activities related to a project.
We include defining the scope of the project, identifying the requirements, preparing the budget, organizing the project team, scheduling the work, monitoring progress, evaluating results, and closing down the project.
How can a manager motivate employees?
Motivation is the desire for success.
Doing something that is enjoyable can help you get motivated.
Or you can get motivated by seeing yourself making a contribution to the success of the organization.
For example: If you want to be a doctor, you might find it more motivating seeing patients than reading medical books all day.
Motivation comes from within.
Perhaps you have a strong sense to give back, for example.
You may even find it enjoyable to work hard.
Ask yourself why you feel so motivated.
Then, consider ways you could improve your motivation.
How does a manager learn to manage?
It is important to have good management skills.
Managers must continuously monitor the performance levels of their subordinates.
You should immediately take action if you see that your subordinate is not performing as well as you would like.
You must be able to spot what is lacking and how you can improve it.
What are the five management methods?
Each business has five stages: planning, execution and monitoring.
Setting goals for the future is part of planning. Planning includes setting goals for the future.
Execution happens when you actually do the plan. It is important to ensure that everyone follows the plans.
Monitoring is a way to track progress towards your objectives. This should involve regular reviews of performance against targets and budgets.
Each year, reviews are held at the end. They provide an opportunity to assess whether everything went well during the year. If not, then it may be possible to make adjustments in order to improve performance next time.
Evaluation takes place after the annual review. It helps identify what worked well and what didn't. It also gives feedback on how well people did.
Statistics
- Hire the top business lawyers and save up to 60% on legal fees (upcounsel.com)
- The profession is expected to grow 7% by 2028, a bit faster than the national average. (wgu.edu)
- Our program is 100% engineered for your success. (online.uc.edu)
- Your choice in Step 5 may very likely be the same or similar to the alternative you placed at the top of your list at the end of Step 4. (umassd.edu)
- The average salary for financial advisors in 2021 is around $60,000 per year, with the top 10% of the profession making more than $111,000 per year. (wgu.edu)
External Links
How To
How is Lean Manufacturing done?
Lean Manufacturing uses structured methods to reduce waste, increase efficiency and reduce waste. These processes were created by Toyota Motor Corporation, Japan in the 1980s. The primary goal was to make products with lower costs and maintain high quality. Lean manufacturing is about eliminating redundant steps and activities from the manufacturing process. It consists of five basic elements: pull systems, continuous improvement, just-in-time, kaizen (continuous change), and 5S. Pull systems involve producing only what the customer wants without any extra work. Continuous improvement means continuously improving on existing processes. Just-in–time refers when components or materials are delivered immediately to their intended destination. Kaizen refers to continuous improvement. It is achieved through small changes that are made continuously. Finally, 5S stands for sort, set in order, shine, standardize, and sustain. These five elements can be combined to achieve the best possible results.
The Lean Production System
Six key concepts are the basis of lean production:
-
Flow - focuses on moving information and materials as close to customers as possible.
-
Value stream mapping - break down each stage of a process into discrete tasks and create a flowchart of the entire process;
-
Five S’s - Sorted, In Order. Shine. Standardize. And Sustain.
-
Kanban – visual signals like colored tape, stickers or other visual cues are used to keep track inventory.
-
Theory of constraints: identify bottlenecks in your process and eliminate them using lean tools, such as kanban board.
-
Just-in time - Get components and materials delivered right at the point of usage;
-
Continuous improvement - incremental improvements are made to the process, not a complete overhaul.